Causes of hydrogen embrittlement in valves [Part 2 of 4]
Welcome to the second delivery of our hydrogen embrittlement series. In this follow-up piece, our talk with Materials Testing Institute’s expert Brian Kagay turns to a new topic that complements part I’s basics of H2 embrittlement and its effects on valves.
Here, the focus is on the causes behind valve embrittlement by H2. We also go over the enabling factors, how they impact the welding process, and the ways to spot affected materials.
Without further ado, here’s part II of the interview.
Table of contents:
I. Part: >> Hydrogen embrittlement of valves and what it means. <<
II. Part: >> Causes of hydrogen embrittlement in valves. <<
III. Part: >> Effects of hydrogen embrittlement on different valve materials. <<
IV. Part: >> Hydrogen embrittlement prevention & control. <<
What are the possible causes of hydrogen embrittlement in valves?
External hydrogen embrittlement could simply be caused by exposure to pressurized hydrogen gas. Pure hydrogen gas or hydrogen could be blended with another gas, such as natural gas, or pumped through a system, and in both cases the material would end up absorbing hydrogen from the fluid. Another possibility is from electrochemical reactions. Here the metal normally functions as a cathode and corrosion processes cause the production of hydrogen on the metal surface. An example of this would be cathodically protected components in subsea environments.
For internal hydrogen embrittlement, there are also many different ways in which hydrogen can enter the valve material before the valve is put into service. Welding, electroplating, galvanizing or pickling processes can all intervene.
What factors can affect hydrogen embrittlement of valves?
For hydrogen embrittlement to occur in a valve three critical elements are required: ( 1 ) a source of hydrogen, ( 2 ) a stress, and ( 3 ) a susceptible material!
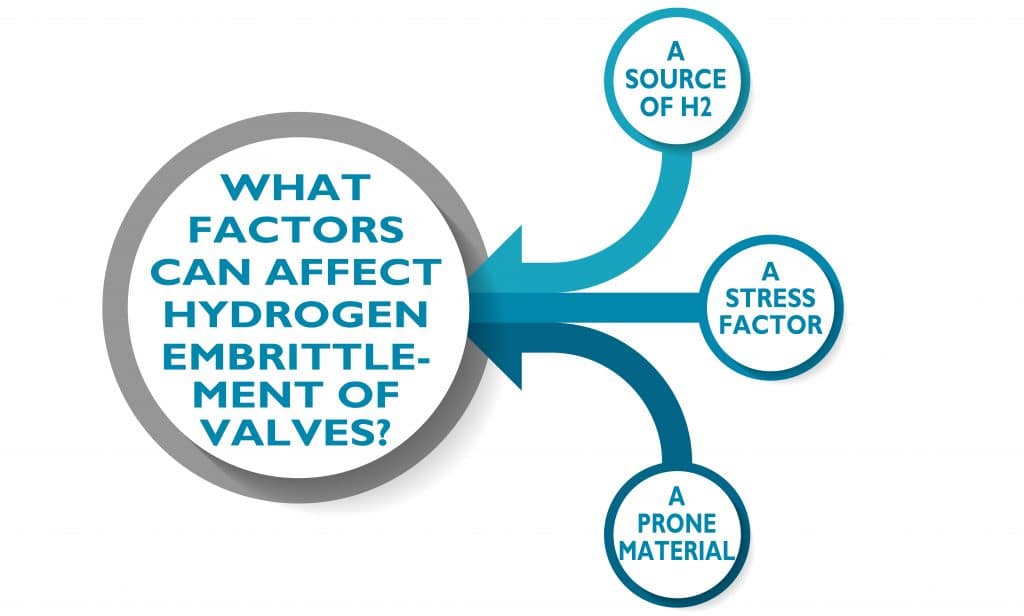
We already discussed some of the possible sources of hydrogen. The stress could be a tensile stress or a cyclic stress, such as from pressure cycling. Residual stresses from manufacturing can also be sufficient to cause hydrogen embrittlement. There are also many factors that determine whether a material is susceptible to hydrogen embrittlement, including the microstructure and presence of impurities.
Beyond these three critical elements, there are other factors that can affect hydrogen embrittlement. Temperature, for example, is a very important parameter to monitor for hydrogen embrittlement. Many steels and nickel-base alloys are most susceptible to hydrogen embrittlement from room temperature and down to -50 °C. Surface roughness can also play a role, since hydrogen cracks can normally form easier on a rougher surface than on a smoother surface.
In valves for hydrogen applications, welding plays an important role. Can you talk about the key factors to focus on in the topic of welding, regarding H2 embrittlement?
Hydrogen is a very application- and component-specific element. So, a good design and material selection approach is prominent to avoid hydrogen embrittlement in welding.
In welds, H2 can be absorbed during the welding process, so from the get-go, a main aspect is that proper welding procedures are followed to minimize hydrogen absorption. In terms of the potential for hydrogen embrittlement due to hydrogen absorbed from the application environment, it is important to consider that a weld will have a divergent microstructure to the base material. The different phases in the weld microstructure can affect the material’s susceptibility to hydrogen embrittlement.
The other factor is the strength of the material. In a weld, both weld metal and a heat-affected zone are present. Each one has different strengths and levels of residual stress, which can affect the potential for hydrogen embrittlement. A post welding heat treatment is a common and successful method for relieving the stress at the weld and can also cause desorption of hydrogen that was present after the welding process. The application of a post-weld heat treatment will depend both on the material welded and how it was welded.
Are there other manufacturing aspects that valve producers should keep in mind?
Manufacturers use cleaning and coating processes that are potential sources of hydrogen and can lead to internal hydrogen embrittlement.
Forming processes, such as bending, also bring new residual stresses into the valve. These residual forces should be accounted for, by the manufacturer, from the design stage. The same goes for any stress concentrator or defect where a crack can form.
Are there ways to identify the occurrence of hydrogen embrittlement?
For sure! The best way to identify hydrogen embrittlement is based on the observed fractures. Certain forms of hydrogen embrittlement, result in very recognizable features. Hydrogen blistering on the surface of a metal is rather unmistakeable. Other times electron microscopy is required to observe the fracture surface of the failed part and hydrogen embrittlement can be identified by comparison to fractures formed in laboratory testing.
A measurement of hydrogen in the material can also be made from a failed component; however, since hydrogen can quickly diffuse out of the metal when it is taken out of the hydrogen environment, there may be no hydrogen left!
Outro
Part II of our hydrogen embrittlement series left us with many parting thoughts:
- There are two lead causes for external H2 embrittlement in valves: ( 1 ) absorption after exposure to pressurized hydrogen, and ( 2 ) electrochemical reactions akin to producing hydrogen on the metallic surface.
- The causes for internal H2 embrittlement in valves are likely to occur at the manufacturing stage. More specifically during the welding, electroplating, galvanizing, or pickling processes.
- H2 embrittlement can only ensue if this triangle of elements participates: ( 1 ) source of hydrogen, ( 2 ) stress, and ( 3 ) susceptible material.
- To reduce the possibility of H2 absorption by the material during welding, manufacturers must follow the protocols strictly. Moreover, they must consider, when applicable, adding stress leveling methods such as post-weld heat treatment (PWHT). Though it is more costly, it’s the safest bet to avoid microstructure changes that lead to material vulnerability and then failure.
- Finally, there are several methods to tell if a material is embrittled. One of them is spotting a fracture or surface blistering through observation. Others are more specialized and may require electron microscopy and hydrogen lab testing.
Look forward to our next delivery, part III of the series. We’ll address the effects of hydrogen embrittlement on different valve materials.
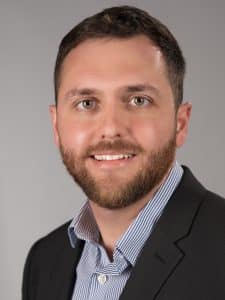
Dr. Brian Kagay
Brian Kagay is a scientist in the Influence of Hydrogen team at the Materials Testing Institute at the University of Stuttgart. His primary research focus is the effect of hydrogen on the mechanical properties and fracture modes of structural alloys. Much of his research has been concerned with understanding the relationship between microstructure and the effects of hydrogen on mechanical behavior, as well as developing test methods for determining mechanical properties in hydrogen environments. He received his Ph. D in Metallurgical and Materials Engineering from Colorado School of Mines, where he studied the effects of hydrogen on nickel-base alloys for oil and gas applications. He was also a postdoctoral appointee in the Hydrogen Effects on Materials Laboratory at Sandia National Laboratories and studied the influence of hydrogen on the fatigue properties, fracture resistance, and deformation mechanisms of stainless steels and pressure vessel steels.
Image Source: © phonlamaiphoto (Adobe Stock), kuliperko (Adobe Stock) & AS-Schneider