Effects of hydrogen embrittlement on different valve materials [Part 3 of 4]
Here is the third part of our hydrogen embrittlement series with special guest Materials Testing Institute’s expert Brian Kagay. In part II, we addressed the causes of hydrogen embrittlement in valves. So, naturally, in this installment, our conversation flowed toward the effects of embrittlement by H2 in different types of valve materials.
Hydrogen doesn’t affect all materials in the same way. So, it became genuinely important for us to touch base on specificities about hydrogen embrittlement in metallic and non-metallic structures to measure the effect on valves.
Let’s begin with part III.
Table of contents:
I. Part: >> Hydrogen embrittlement of valves and what it means. <<
II. Part: >> Causes of hydrogen embrittlement in valves. <<
III. Part: >> Effects of hydrogen embrittlement on different valve materials. <<
IV. Part: >> Hydrogen embrittlement prevention & control. <<
What metals are more susceptible to hydrogen embrittlement?
The susceptibility of a material is dependent on the use as well as the chosen application. But, as a general approach, when it comes to vulnerability to hydrogn embrittlement, the metals can be grouped into two categories:
- Those susceptible to hydrogen. Most metals are sensitive to hydrogen embrittlement; however, the severity of the embrittlement varies. High strength metals with a body-centered cubic lattice, such as martensitic steels, are severely embrittled, but metals with a face-centered cubic lattice, such as nickel-base alloys, can also be embrittled by hydrogen.
- Those which are negligibly embrittled. This group is much smaller and consists of only certain metals with a face-centered cubic lattice. A case in point for the type is aluminum alloys.
Does hydrogen embrittlement occur in all steels?
Most steels are embrittled by hydrogen; however, some austenitic stainless steels, which contain Cr and Ni, are insensitive to hydrogen embrittlement to a great extent. Therefore, these steels are among the standard materials used in hydrogen technology. In the stainless-steel family, a higher nickel content generally results in greater resistance to hydrogen embrittlement.
What factors determine how susceptible a material is to hydrogen embrittlement?
Material strength, cleanliness, and microstructure all play a role in hydrogen embrittlement susceptibility. Generally, higher strength materials are more susceptible than lower strength materials. The presence of defects, such as oxide inclusions, and impurities, such as sulfur and phosphorous, can also increase hydrogen embrittlement susceptibility.
A material’s microstructure can also affect hydrogen embrittlement in many ways. Certain phases or precipitates may act as crack initiation sites and increase hydrogen embrittlement susceptibility, while other precipitates may trap hydrogen and therefore have the opposite effect. The grain size and dislocation density can also play a role.
Crystal structure also affects how hydrogen behaves in a material. Hydrogen diffuses must faster through body-centered cubic (bcc) steels than through face-centered cubic (fcc) steels, but a much greater hydrogen concentration can be reached in fcc steels than in bcc steels.
Finally, the source of hydrogen can determine whether hydrogen embrittlement will occur. Aluminum alloys are essentially insensitive to dry hydrogen gas, but small amounts of moisture can cause hydrogen to be absorbed and result in hydrogen embrittlement.
Are metals sensitive to H2 attacks allowed in hydrogen engineering?
Certainly! Though some metals, such as high strength steels, are less resistant to hydrogen embrittlement, they can still be implemented in hydrogen applications. The core aspect around the application of these materials is to ensure a suitable working stress level for the component. That way, the material can stay below the threshold point defined through testing and the initiation or propagation of cracks is suppressed.
Are there potential hydrogen embrittlement effects in nonmetallic materials?
There are some concerns on the hydrogen embrittlement process of polymeric materials. Polymeric products, such as rubbers or o-rings, absorb large amounts of hydrogen. At a depressurization stage, with temperature changes, damage can occur due to the high concentration of H2 already present, which leads to blisters and swelling. An answer to the issue is to put in place a controlled temperature depressurization.
Though not a form of embrittlement, the rate of diffusion of hydrogen through polymers can also be a concern for certain applications. There is much ongoing research on hydrogen effects on polymeric materials, including their behavior under mechanical loading.
Outro
And so, we leave part III behind with these takeaways on the effect of hydrogen embrittlement in materials:
- The degree of susceptibility to H2 embrittlement splits materials into two major groups:( 1 ) vulnerable (high-strength metals with a body-centered cubic lattice), and ( 2 ) non-vulnerable (some face-centered cubic lattice metals).
- Among the vulnerable materials are stainless steel, martensitic steels, nickel-base alloys, and non-metallic polymers.
- Non-vulnerable materials include aluminum alloys and austenitic stainless steels high in Cr and Ni content.
- Insensitive materials to embrittlement by H2 are fit for use in hydrogen applications.
- The deployment of vulnerable materials in H2 technologies is also possible as long as a suitable working stress level is secured.
- Material strength, cleanliness, and microstructure determine a material’s sensitivity to hydrogen embrittlement.
- The presence of oxide inclusions and impurities raises the chances of embrittlement by H2 in a material.
Don’t miss out on our next and final delivery of this hydrogen embrittlement series. In part IV, we will share prevention and control mechanisms to protect valves against H2 embrittlement and address the hot topic that started it all: blended operations!
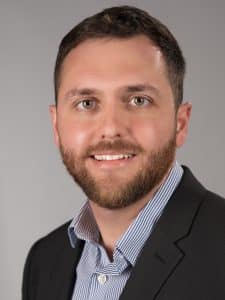
Dr. Brian Kagay
Brian Kagay is a scientist in the Influence of Hydrogen team at the Materials Testing Institute at the University of Stuttgart. His primary research focus is the effect of hydrogen on the mechanical properties and fracture modes of structural alloys. Much of his research has been concerned with understanding the relationship between microstructure and the effects of hydrogen on mechanical behavior, as well as developing test methods for determining mechanical properties in hydrogen environments. He received his Ph. D in Metallurgical and Materials Engineering from Colorado School of Mines, where he studied the effects of hydrogen on nickel-base alloys for oil and gas applications. He was also a postdoctoral appointee in the Hydrogen Effects on Materials Laboratory at Sandia National Laboratories and studied the influence of hydrogen on the fatigue properties, fracture resistance, and deformation mechanisms of stainless steels and pressure vessel steels.
Image Source: © phonlamaiphoto (Adobe Stock), kuliperko (Adobe Stock) & AS-Schneider