Hydrogen embrittlement prevention and control [Part 4 of 4]
At last, we reached the final delivery of our hydrogen embrittlement series. In part IV, we continue our interview with Material Testing Institute’s expert, Brain Kagay. Before, in part III, he shared precise insight into the effect of hydrogen embrittlement in different materials (metallic and non-metallic).
As a manufacturer, we are well aware that plant operators, engineers and maintenance personnel are very interested in knowing the mechanisms to prevent and control hydrogen embrittlement. So we asked Brian Kagay.
In addition, Brian Kagay shares other important information about the future blended operations of natural gas and hydrogen in the German natural gas grid and about the next steps in researching the effects of hydrogen on materials.
Here’s what Brian Kagay had to say in our final part of the interview!
Table of contents:
I. Part: >> Hydrogen embrittlement of valves and what it means. <<
II. Part: >> Causes of hydrogen embrittlement in valves.<<
III. Part: >> Effects of hydrogen embrittlement on different valve materials.<<
IV. Part: >> Hydrogen embrittlement prevention & control. <<
How can hydrogen embrittlement be prevented?
We discussed earlier how there are three critical elements required for hydrogen embrittlement: a source of hydrogen, a stress, and a susceptible material. The key to hydrogen embrittlement prevention is limiting or even eliminating one or more of these elements.
Decreasing hydrogen gas pressure or preventing electrochemical reactions that produce hydrogen are examples of limiting the source of hydrogen. Applying a coating can also prevent hydrogen absorption, but the coating must always remain intact to be effective. There is also research that shows that small amounts of oxygen added to hydrogen gas can passivate the material and prevent hydrogen embrittlement, but this method can be difficult to implement. In terms of internal hydrogen embrittlement, proper manufacturing and welding techniques are key to preventing hydrogen ingress prior to service.
Component design is essential to keep stresses below an acceptable threshold for many hydrogen applications. Tensile and fatigue loading, as well as residual stresses can all lead to hydrogen embrittlement and must be accounted for. Stress concentrators, such as threads and joints, also must be properly designed to limit the applied stresses. With proper design even high strength materials that are susceptible to hydrogen embrittlement can be used in some hydrogen applications.
The final critical method of hydrogen embrittlement prevention is material selection. If the stresses and source of hydrogen cannot be limited, then a more resistant material may need to be used. On the other hand, even though some materials are more resistant to hydrogen embrittlement than others, it is not always necessary to use the most resistant material. It really depends on the service, components, and stresses. There’s also the matter of pricing. Should you go with a more expensive but resistant material or a cheaper material but with a more robust design? These are all factors to analyze, and there’s no simple answer.
Non-destructive evaluation prior to service is also important for many applications. The main idea is that the non-destructive evaluation can detect flaws of a certain size, and the component can be designed so that failure won’t occur due to flaws that are smaller than the detection limit of the non-destructive evaluation technique.
All in all, development of standards for materials selection and design through continued testing and research is an important part of preventing hydrogen embrittlement.
Finally, we come to a highly “hot” issue: Material embrittlement when hydrogen is mixed into natural gas. In the project "H2 Substitution II", a research team from the Institute for Materials Application at the TH Cologne examined how hydrogen affects industrial plants. The result is: A natural gas-hydrogen mixture poses no danger to industrial plants. Do you agree?
In some applications, a natural gas-hydrogen mixture may not affect material embrittlement. However, that’s dependent on the materials used and the operating conditions—particularly temperature.
Research has already shown that small amounts of hydrogen blended with natural gas have an effect on steels at or near room temperatures. Just a small fraction of H2 in natural gas is powerful enough to decrease the fracture toughness of steel pipelines. The effect of blending hydrogen with natural gas on materials appears to be based on the partial pressure of H2, so the amount of hydrogen in the mixture is comparable to having pure hydrogen at that pressure. For example, let’s say the partial pressure of H2 in a blend is 10 bar. Then, its effect will be similar to having a pure hydrogen environment at 10 bar pressure. Steels are normally less susceptible to hydrogen embrittlement at temperatures above room temperature so hydrogen blends likely do not pose as much of a threat to components operated at elevated temperature; however, further research on this topic is necessary.
Currently hydrogen-related research or industrial projects
To wrap up the interview, we asked Brian Kagay about the current things on his plate. His answer gave us reasons to look forward to further news about the work at Materials Testing Institute University of Stuttgart in the area of hydrogen embrittlement.
Are you currently working on hydrogen-related research or industrial projects? If so, can you briefly present them and explain their focus?
Yes, we have many ongoing research projects with our industrial partners and other research institutions related to hydrogen across a broad line of sectors. We are working on projects focused on assessing the effects of hydrogen on:
- components for fuel cell cars and hydrogen fueling stations;
- pipelines and pipeline steels;
- materials for high temperature applications in power plants;
- additively manufactured materials.
We are also pursuing projects on the effects of hydrogen at cryogenic temperatures, including in liquid hydrogen, as well as high temperatures for aerospace applications.
As you can see, we are focused on a wide range of research projects across many industries that use hydrogen. We are interested in understanding the relationship between material and environmental parameters and hydrogen embrittlement, as well as developing new testing methods.
The recent increase in political interest in hydrogen technologies has pushed us to think about the influence of hydrogen on materials in new industries and applications, and I find this to be very exciting.
Outro
Across this four-part hydrogen embrittlement series, our interview with Brian Kagay conveyed relevant issues for valve manufacturers, designers, and operators. To conclude, we summarized the main takeaways. Just as they were discussed from beginning to end.
On hydrogen embrittlement:
- Hydrogen embrittlement is an aggressive process that deteriorates the mechanical integrity of materials.
- Materials affected by H2 embrittlement suffer from loss of ductility, fracture toughness, or fatigue life. This change in material behavior leads to the formation of cracks and eventual failure.
- The most common type of H2 embrittlement is due to stress. It manifests internally, through H2 absorption, or externally, due to environmental factors.
- H2 embrittlement by chemical reaction can also damage materials. Hydride formation is a good example of this case.
- Most metals are sensitive to hydrogen embrittlement. High strength steels with a body-centered cubic lattice, are particularly embrittled, but other metals with a face-centered cubic lattice can also suffer from hydrogen embrittlement. A few metals, such as aluminum alloys and some austenitic stainless steels, are negligibly embrittled by hydrogen.
- Though many materials are not resistant to H2, they can still be part of a hydrogen application. Ensuring a suitable working stress level for the piece is mandatory.
- Polymeric materials, such as rubbers or o-rings, absorb large amounts of hydrogen. This makes them susceptible to H2 damage during depressurization.
On causes of hydrogen embrittlement of valves:
- Valves can be damaged by hydrogen embrittlement when atomic hydrogen forms on a metallic surface and diffuses into the material. The source of hydrogen can be gaseous hydrogen or a result of electrochemical reactions.
- Improper manufacturing can cause hydrogen to be absorbed prior to service and can lead to failure due to hydrogen embrittlement.
- For a valve to be embrittled by hydrogen, three factors must be present: stress, a source of hydrogen, and a susceptible material!
- Hydrogen can be absorbed directly during welding of a valve. More importantly the microstructure and residual stresses present in a weld and the heat-affected zone can increase susceptibility to hydrogen embrittlement.
- A post welding heat treatment is a common and successful method for relieving the residual stress created by welding.
- Additional factors, such as temperature and surface roughness, can also affect the likelihood of hydrogen embrittlement occurring.
On hydrogen embrittlement prevention and control:
- Hydrogen embrittlement can be mitigated by limiting or removing one of three key elements: a source of hydrogen, stress, and a susceptible material.
- Adjusting operating conditions, applying a coating, or even introducing a small amount of oxygen into hydrogen gas can decrease the hydrogen available to cause hydrogen embrittlement.
- Proper design, including consideration of stress concentrators, as well as stress-relieving heat treatments are important strategies.
- Materials selection is extremely important. The amount of hydrogen and the applied stresses will influence how resistant of a material must be used.
On the possibility of H2 embrittlement in blending operations:
- A natural gas-hydrogen mixture may or may not affect material embrittlement. It's all dependent on the materials used and operative conditions defined—particularly temperature.
- To overcome the bottlenecks of a potential blending hydrogen scenario, the best approach to follow is apply a good design, factor-in the stresses applied, and make a great material selection.
We hope this whole series was of service to the industry. Even more, as Germany prepares for blended operations.
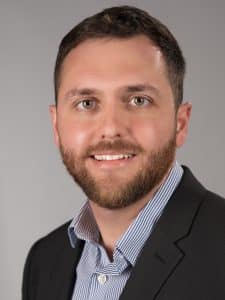
Dr. Brian Kagay
Brian Kagay is a scientist in the Influence of Hydrogen team at the Materials Testing Institute at the University of Stuttgart. His primary research focus is the effect of hydrogen on the mechanical properties and fracture modes of structural alloys. Much of his research has been concerned with understanding the relationship between microstructure and the effects of hydrogen on mechanical behavior, as well as developing test methods for determining mechanical properties in hydrogen environments. He received his Ph. D in Metallurgical and Materials Engineering from Colorado School of Mines, where he studied the effects of hydrogen on nickel-base alloys for oil and gas applications. He was also a postdoctoral appointee in the Hydrogen Effects on Materials Laboratory at Sandia National Laboratories and studied the influence of hydrogen on the fatigue properties, fracture resistance, and deformation mechanisms of stainless steels and pressure vessel steels.
Image Source: © phonlamaiphoto (Adobe Stock), kuliperko (Adobe Stock) & AS-Schneider