How DBB valves help meet offshore size and vibration restrictions
Offshore is without question one of the most challenging working environments for the oil and gas sector. The harsh weather conditions and remote location add a unique layer to everyday operations. Having impeccable timing takes on a whole new meaning in maintenance tasks. I’m touching the ground on this subject because AS-Schneider recently had me assist a client with their valve technology. The project was for the gas lift compression module of a floating production, storage, and offloading (FPSO) vessel in West Africa. We not only completed the job but also got to learn genuinely valuable lessons worth sharing. Thus, I’m happy to have the chance to do so today through this blog. Here’s the story of how we helped a dear customer, an upstream contractor, obtain double block and bleed (DBB) valves that met the site’s tight constraints on space, weight, and vibration. Read along!
Facing a unique challenge involving DBB valves for an offshore gas lift compression module
The level of mastery needed to work offshore is both intimidating and inspiring at the same time. So, when our client reached out to ask for help, we prepared to rise to the occasion. The project was already underway. Still, several internal reviews had shown that valve technology needed to be looked at from a fresh perspective. As our customer had predicted, changes to the original design would follow.
We started right away by assessing the early configurations. It took a lot of blood and sweat, especially when addressing the special offshore requirements. Certifications and paint specs were a pain to go through. At this point, being seasoned suppliers and creators of tailored solutions drove us to put the final nail in the coffin sooner than expected. Thanks to our know-how, we found a suting DBB valve design! There’s no doubt that they would work well with the FPSO’s gas lift compression module’s tight restrinctions on space, weight, and vibration.
“Life is a box of chocolates; you never know what you’re going to get.” The same philosophy applies all too often to a project
So, as I was saying earlier, offshore can be tricky. The project was moving smoothly. Design deliverables, like data sheets and drawings, were carefully prepared according to the specifications. Both the contractor and the operator, as the final client, were feeling happy and confident about the progress. Then, two unexpected alarms arose:
#1
For this project, serious space constraints and reduced weight were two factors that mattered. They were part of the secret sauce for improving the piping layout and being able to fit the gas lift compression module on the FPSO ship. That meant, the arrangement of equipment and accessories had to fit in the predetermined space and dimensions already in place in the integrated skid-mounted module.
#2
The other surprising issue was related to the module’s gas compressor. Manufacturers now had to consider the impact of potential vibration in field measurement devices and process valves from the heavy-duty and high-pressure rotating equipment.
Panic mode took over! The threat of going behind schedule and having to send engineers back to the project’s early stages was too real. A new budget overview was in the cards.
In times of uncertainty, bring in an expert friend. It might just save your project
When our contractor friend got in touch with AS-Schneider, the concern was palpable. As a customer-focused, innovative company with a proven track record in instrumentation devices and double block and bleed valves for oil and gas applications, we felt ready and able to do the job. Our design team got up to speed on what was needed to solve their problem. We did it in three steps:
1st
…. we overviewed our DBB solutions. Soon, we noticed there was a sturdy model that could meet the specs. We just had to customize it according to the new space, weight, and vibration requirements.
2nd
…. having spotted a solution, we entered the design stage. It was to re-engineer our 1-pc DCZ series for DBB valves. The new arrangement included an OS&Y bonnet paired with the shortest face-to-face DBB valves possible.
3rd
…. we could tell the design wasn’t finished. Our team completed it by tailoring the bore size of the valves to make it match the original design.
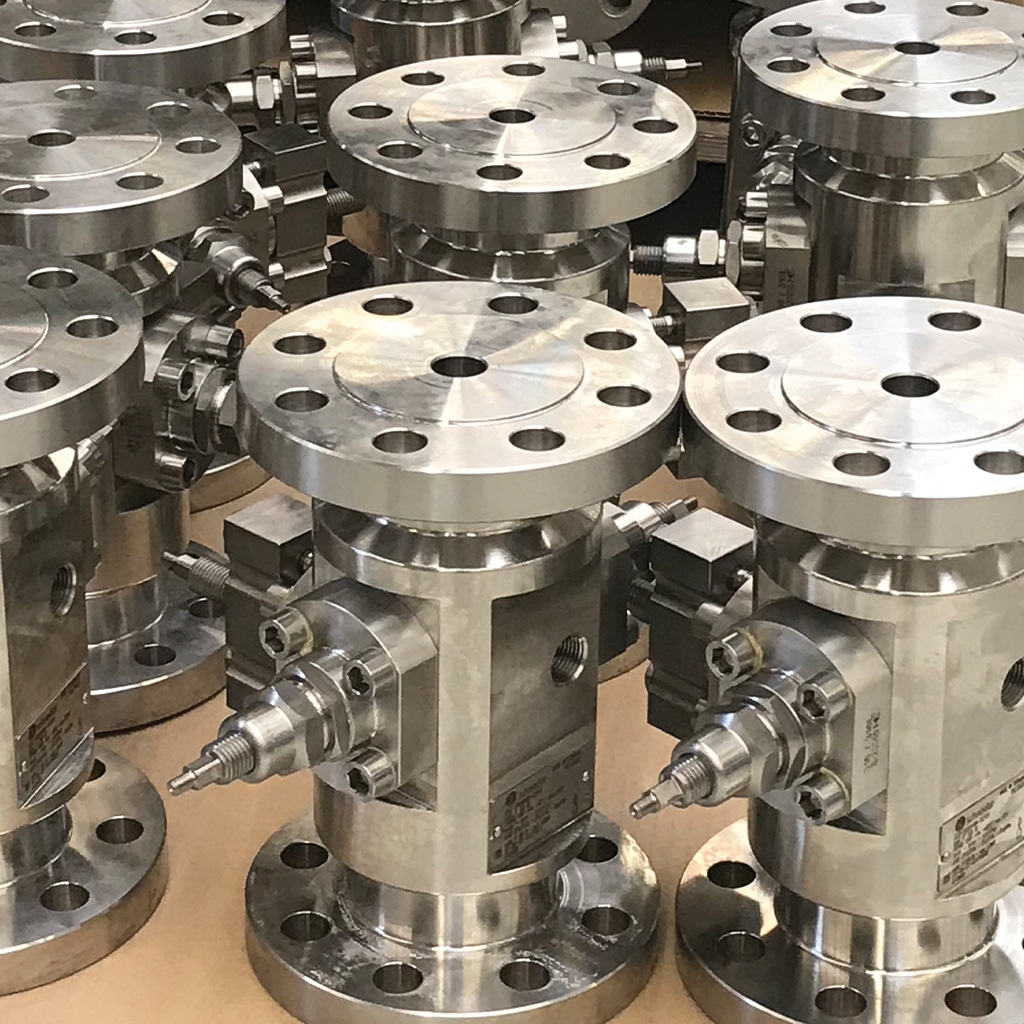
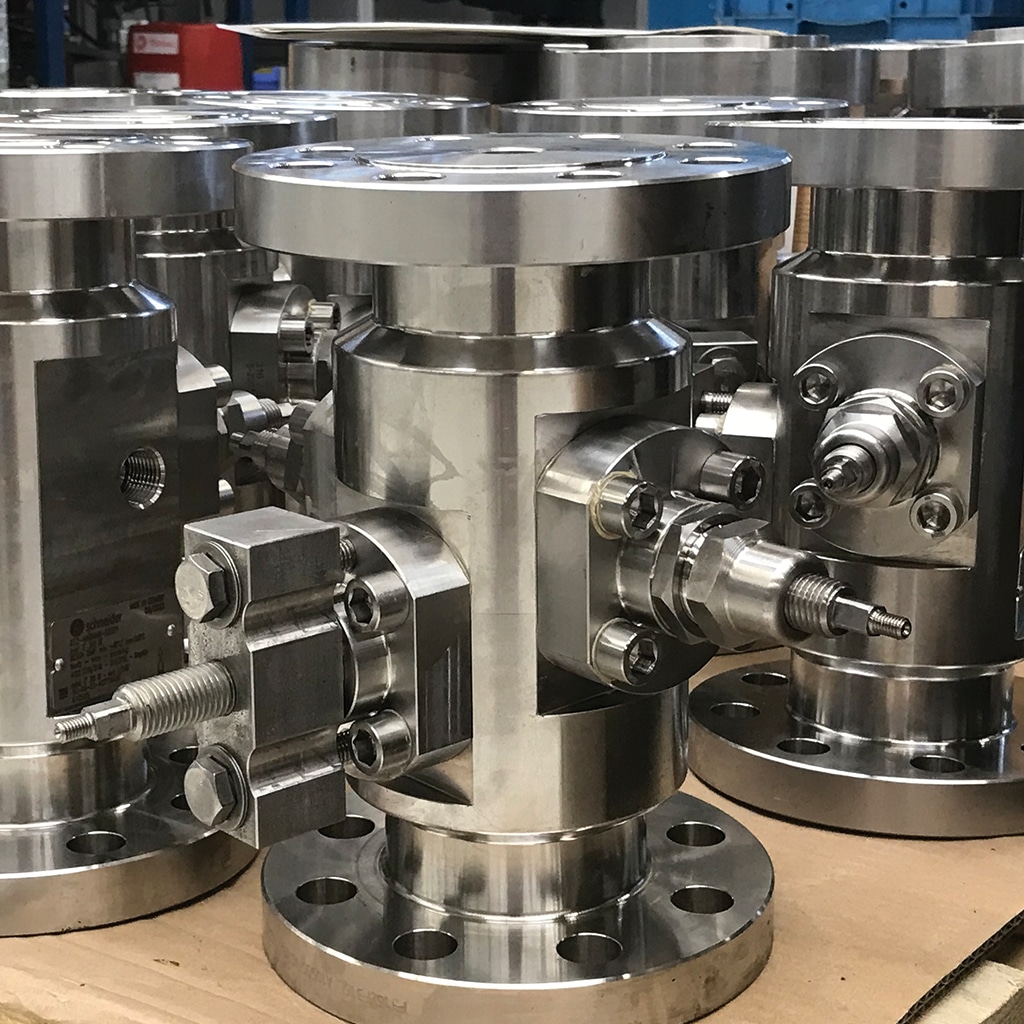
Through these three steps, we fully ensured the general specifications were satisfied. Our customer was pleased with our solution. Now it was time to look for the approval of the operator as the end user he had the final word on our proposal.
Good news came in. The proposal passed without hesitation! The operator walked out feeling relieved. They were an impressed and happy customer once again.
The work on this beauty of a gas lift compression module was back on full steam.
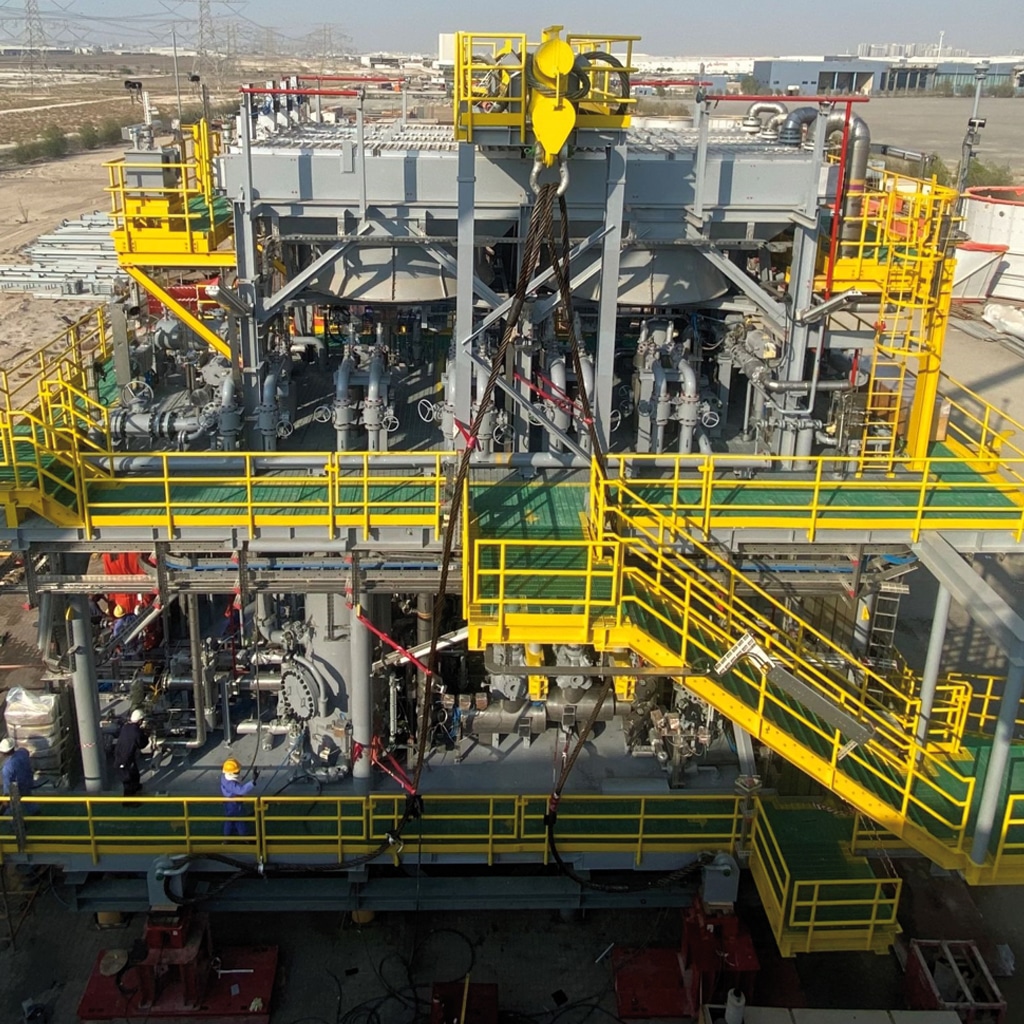
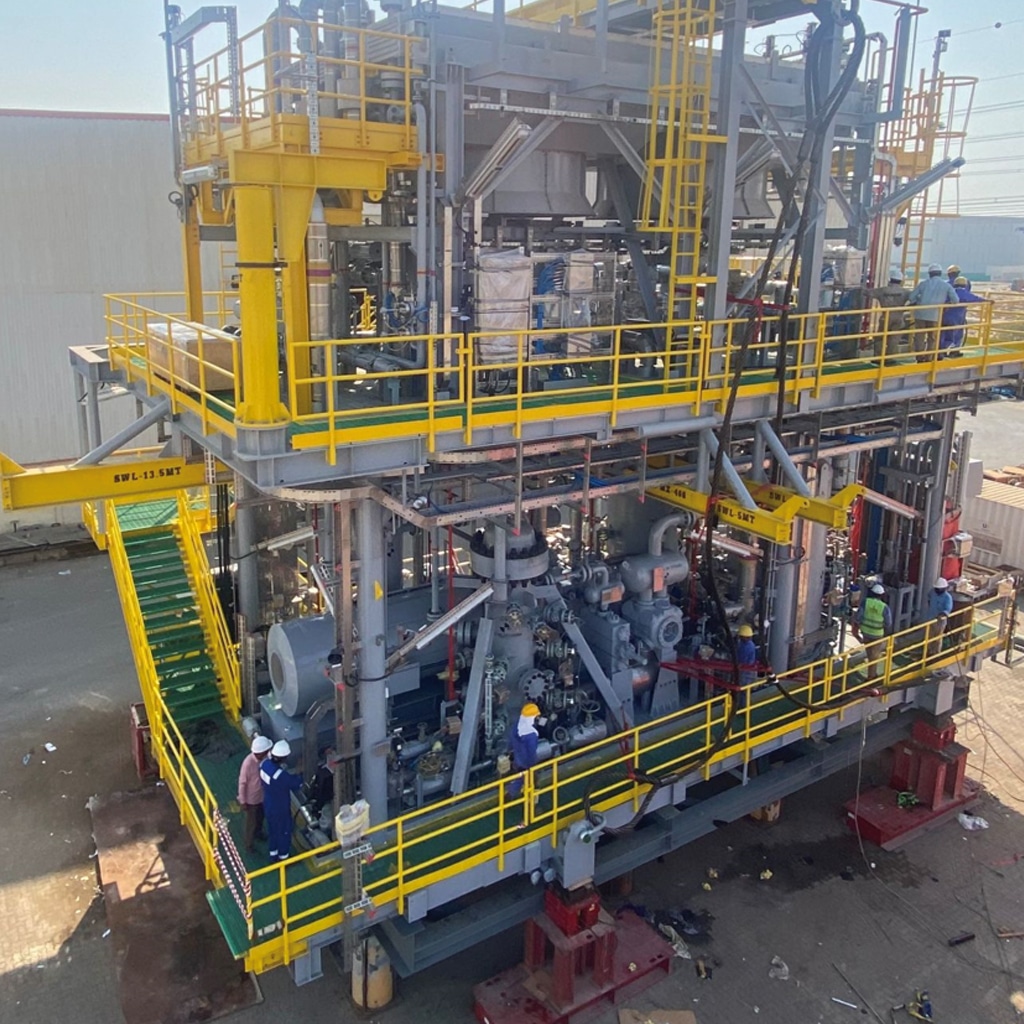
Projects are, to me, living, evolving organisms. Most times, the input and output remain unaltered, but what goes in between can change and have an impact on the original structure. That is what happened in this offshore project for a gas lift compression module to be installed on an FPSO. Halfway through, new sizing and weight requirements came into place, along with vibration concerns from the main equipment. What was left to do? Adapt and move forward with the help of a trusted partner—just as our customer did. They smartly managed to find a way to get out of time pressure by ensuring a winning solution from an expert product supplier.
I can only speak for AS-Schneider when I say that coming up with out-of-the-box, impossible-seeming solutions for clients is rewarding and inspiring. We get the same feeling when the project is out of the woods and back on track. That’s among the best parts of our day! It’s what makes all employees at AS-Schneider tick.
A final farewell as I finish off preparations for a repeat order from the same client, a sure sign that they were pleased with our services. What a great feeling!
Until the next time.
Image Source: © AS-Schneider