Is hydrogen embrittlement a threat to valves? Get the answer here! [Part 1 of 4]
Germany is hard at work on becoming a decarbonized region. The country found a scalable solution in hydrogen that favors all parts—the environment, citizens, and industries. To get the H2 initiative started, the government, with the help of the scientific community, is developing several macro projects. The first phase focuses on blended operations that lead to the controlled addition of hydrogen into the existing natural gas grid infrastructure.
Under such a novel context, it is natural to inquire about the potential implications of gas blending. How can the addition of hydrogen affect the existing systems? Is hydrogen embrittlement of materials a possibility? What are the causes? How to prevent it? These are rather important questions raised by plant operators. So, as valve manufacturers, AS-Schneider felt committed to taking action and finding answers. We sent our team to a one-on-one meeting with specialist Dr. Brian Kagay. His work in the prestigious Materials Testing Institute at the University of Stuttgart qualifies him as an expert in this subject. If you are a plant operator, you don’t want to miss out on what he had to say.
Table of contents:
I. Part: >> Hydrogen embrittlement of valves and what it means. <<
II. Part: >> Causes of hydrogen embrittlement in valves. <<
III. Part: >> Effects of hydrogen embrittlement on different valve materials. <<
IV. Part: >> Hydrogen embrittlement prevention & control. <<
Hydrogen embrittlement of valves and what it means
In part I of this hydrogen embrittlement series, our conversation with Brian Kagay focused on the effects of hydrogen on valves and their metallic structure. Though, not first without touching the ground on his journey as a specialist in the field.
Hi, Brian. Can you give us a little bit of background on your journey as a hydrogen embrittlement specialist?
It all started in undergrad school at the University of Florida—I’m originally from the United States. There, I studied Materials Science & Engineering. Then, I went to the Colorado School of Mines for my Ph. D. as part of The Advanced Steel Processing & Products Research Center, focusing on the hydrogen embrittlement of nickel-based alloys. Afterward, I moved to SANDIA National Laboratories in Livermore, California, where I joined the Hydrogen Effects on Materials laboratory. At SANDIA, I studied H2 effects on stainless and carbon steel materials. And now, finally, I’m at MPA (Material Testing Institute University of Stuttgart) as a scientist and researcher to study the effects of hydrogen on metals. It’s been a busy and ever unfolding road.
Moving onto the subject. What is hydrogen embrittlement?
Hydrogen embrittlement is the decrease in ductility of a material due to hydrogen. The condition appears when the hydrogen concentration raises over the limit acceptable by the material. The signs include loss of tensile ductility, fracture toughness, or fatigue life. When the H2 level is too high, it decreases the stress required to form cracks, thus, leading to fracture or premature failure of the material.
What are the types of hydrogen embrittlement?
There are two main forms of hydrogen embrittlement that occur when stress is applied to a material:
- internal hydrogen embrittlement, and
- external or hydrogen environment embrittlement.
For internal hydrogen embrittlement, the material absorbs H2 before a stress is applied. In many cases, the hydrogen is absorbed during steel-making, welding, or electroplating. When the component is then put into service, the combination of H2 and stress can lead to failure.
External hydrogen embrittlement, by contrast, occurs when the material absorbs hydrogen in service. The material goes into service in an environment prone to H2 absorption, and cracks appear. That’s why this form is also called hydrogen environment embrittlement.
There’s also another form of hydrogen embrittlement in which stress isn’t necessarily required. Hydrogen reaction embrittlement can occur when chemical reactions with hydrogen occur inside a material.
An important example of a hydrogen embrittlement reaction is hydride formation. A hydride is a material phase that forms when metals like titanium and vanadium absorb large amounts of hydrogen. The hydride phase tends to be very brittle. So, its presence in the material makes it more susceptible to failure. Similarly, H2 can react with the oxides in copper to cause material weakening. In high-temperature hydrogen attack, hydrogen also affects steel by reacting with carbon to form methane inside the steel. The aftermath of this last scenario leads to intergranular fracture. At last, with high concentrations of hydrogen, atomic hydrogen can recombine to form bubbles of molecular hydrogen in the material and produce hydrogen-induced blister cracking.
How does the concept of hydrogen embrittlement apply to valves?
Hydrogen embrittlement of valves is a realistic occurrence. When a valve is used in a hydrogen-rich environment, atomic hydrogen can form on the surface and be absorbed into the material. The hydrogen will diffuse through the metal lattice and some hydrogen may deposit preferentially at defects or grain boundaries. Depending on the stress on the material, this hydrogen could lead to the formation of cracks and therefore external hydrogen embrittlement would occur.
Hydrogen could also be present in the valve material prior to the valve being put into operation due to improper material processing. If enough hydrogen is present and there are sufficient stresses on the valve, then failure may occur, which would be considered internal hydrogen embrittlement.
Outro
Part I of this hydrogen embrittlement series allowed us to gain a better understanding of how the two forms of hydrogen embrittlement (internal and external) can affect materials and valves. The consequence is the setting for an early failure.
Our conversation with Brian Kagay continues in part II of the interview. There, we’ll go further in the topic by addressing the causes of hydrogen embrittlement in valves, along with the influential factors for occurrence and more.
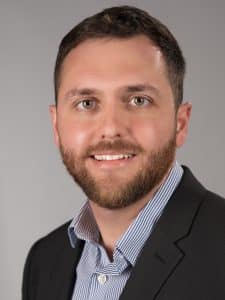
Dr. Brian Kagay
Brian Kagay is a scientist in the Influence of Hydrogen team at the Materials Testing Institute at the University of Stuttgart. His primary research focus is the effect of hydrogen on the mechanical properties and fracture modes of structural alloys. Much of his research has been concerned with understanding the relationship between microstructure and the effects of hydrogen on mechanical behavior, as well as developing test methods for determining mechanical properties in hydrogen environments. He received his Ph. D in Metallurgical and Materials Engineering from Colorado School of Mines, where he studied the effects of hydrogen on nickel-base alloys for oil and gas applications. He was also a postdoctoral appointee in the Hydrogen Effects on Materials Laboratory at Sandia National Laboratories and studied the influence of hydrogen on the fatigue properties, fracture resistance, and deformation mechanisms of stainless steels and pressure vessel steels.
Image Source: © phonlamaiphoto (Adobe Stock), kuliperko (Adobe Stock) & AS-Schneider