Types of valves used in piping and how to classify them
This article presents an overview of valves, their functions and the commonly used types of valves in the industry. The design principle, application areas, benefits and disadvantages of various types of valves are presented. Different methods of valve classification are also discussed to highlight the key considerations in valve selection.
What is a valve?
A valve is a mechanical device used in fluid systems to control, direct, isolate, mix, or regulate the flow or pressure of a fluid, by modifying the passageway through the pipe. When a valve is in the open position, the passageway is unobstructed and the fluid flows in a direction from higher pressure to lower pressure. By partially or fully obstructing the passageway through the valve, the flow can be reduced or completely stopped.
Technically, valves are pipe fittings but due to their critical function, wide variety of types, and operation options they are generally considered separately from other fittings. Valves are often the costliest components of the piping system in a plant; the cost of valves can be as much as 30% of the overall piping cost.
What are the functions of a valve in piping systems?
Valves play a critical role in increasing efficiency, improving quality control, and ensuring safety and reliability of a process. The primary consideration in valve selection is the desired function of the valve. Valves are incorporated into a piping system for one or more of the following reasons:
- Starting or stopping fluid flow
- Throttling flow rates within a piping system
- Regulation of pressure
- Regulation of fluid temperature in a piping system
- Redirecting the flow from one path to another
- Restricting the flow for system balance or to prevent over pressurization
- Prevent reverse flow of fluid
- Stopping the flow in case of a system failure
- Improving safety through relieving pressure or vacuum in a piping system
At the design stage of a manufacturing process or a piping system, engineers generally specify the type of valve suitable for the desired function on the Process and Instrumentation Diagram (P&ID). A P&ID is a schematic illustration of the functional relationship of piping, instrumentation and system components. Different types of valves commonly found on P&IDs are introduced and discusses in the following section.
What are the different types of valves?
The table below lists the different types of valves and their corresponding P&ID symbols. The most commonly used types of valves are gate valves, globe valves, check valves and ball valves.
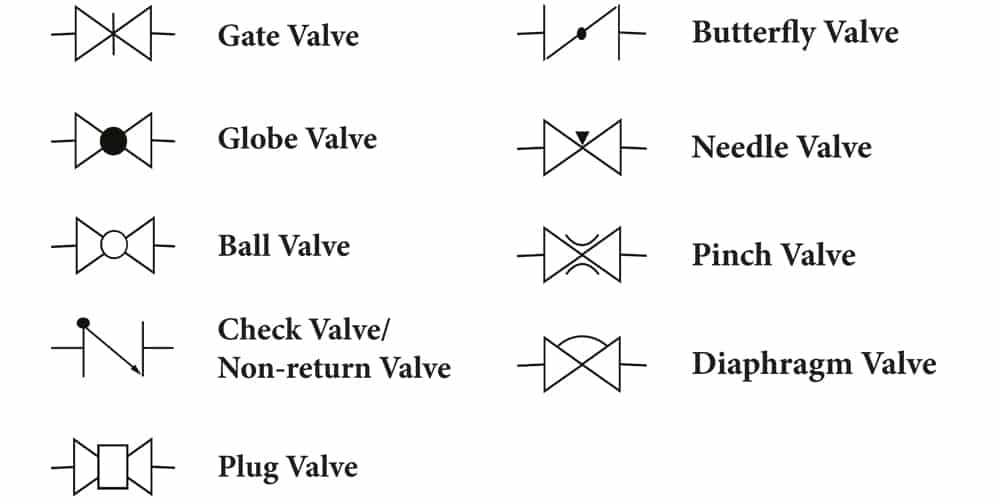
Gate Valve
Gate valves are the most common type of valves found in process plants. The closing gate moves along a linear path to block or allow fluid flow. Gate valves provide good shutoff and are considered suitable for almost all fluid services including air, fuel gas, feedwater, steam, slurries and viscous liquids.

Gate valves are inexpensive and easy to disassemble for maintenance. They offer low fluid resistance due to a straight path that allows the fluid to flow straight through without change in direction.
During use, gate valves are normally kept in either a fully open or a fully closed position as they are not recommended for throttling applications. The valve design makes it difficult to control the flow.
Furthermore, the fluid slapping against a partially open gate can damage the valve. The multi-turn design of these valves makes them unsuitable for applications where rapid operation is desired.
Globe Valve
A globe valve generally has a spherical body that contains a movable plug element and a stationary ring seat. The two halves of the body are separated by an internal baffle. The plug element is connected to an operating hand wheel through a stem. As the wheel is turned, the screw action moves the plug towards or away from the ring seat. Globe valves can be used for stop/start function as well as to regulate fluid flow. They are useful in applications where good flow control is desired and leak tightness is important such as cooling water systems, feedwater and chemical feed systems, and fuel/lubricating oil systems.
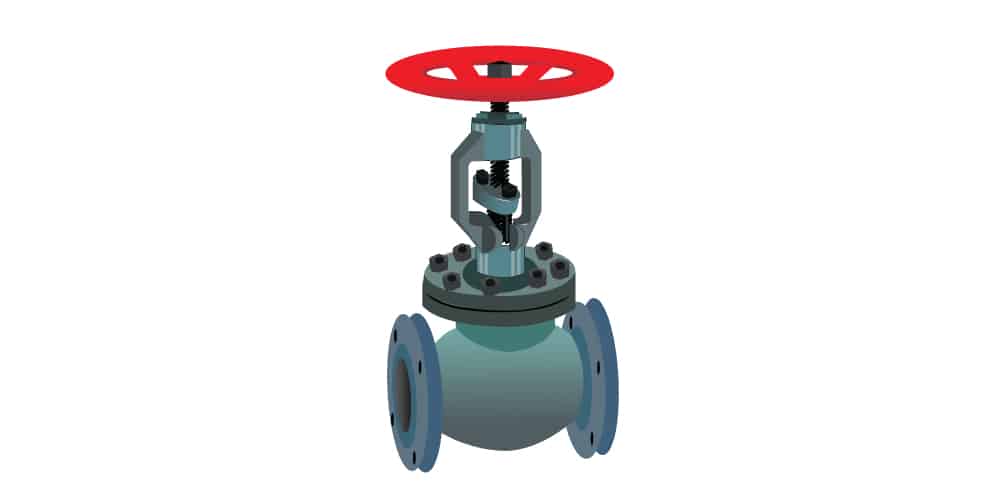
Globe valves cost more than gate valves but provide better shut off and throttling control. The design of these valves forces the fluid to change direction as it flows through; this creates high pressure loss and turbulence. Globe valves are generally heavier than other valves. They are not suitable for fluids containing particles, high viscosity fluids and other mediums that are prone to choking.
Ball Valve
A ball valve uses a hollow ball to stop or allow fluid flow. The perforated ball can be pivoted using the valve handle. When the hole in the ball faces the flow inlet, the fluid flows through. A quarter-turn rotary motion of the valve handle turns the ball by 90° blocking the flow.
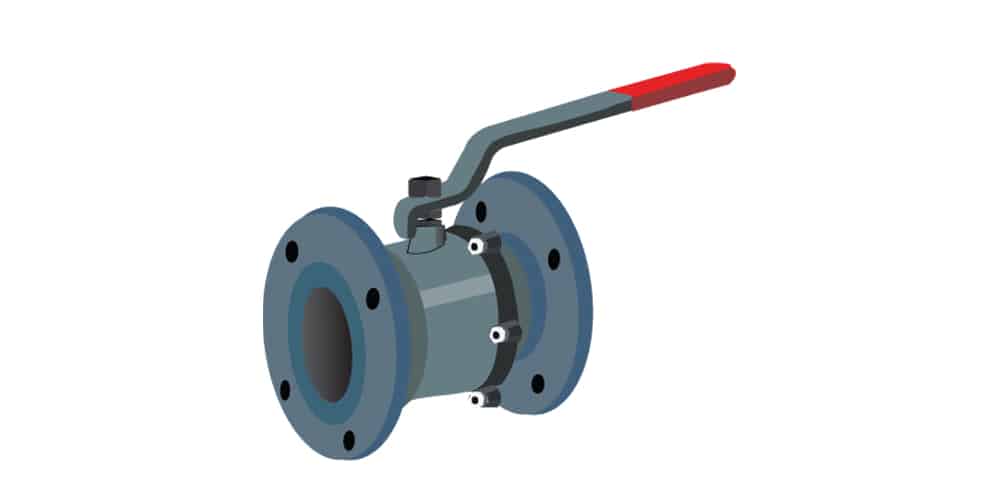
Ball valves are smaller, lighter and cheaper when compared to gate valves of the same size and rating. They allow visual detection of the open or closed state of the valve. In an open state, the handle is aligned with the direction of flow; in a closed state the handle is perpendicular to the flow direction. In addition, ball valves offer ease of operation, high volume flow, high pressure, long service life and possibility of repair of seats and seals without removing the valve body from the line. On the other hand, ball valves are difficult to clean which can lead to contamination. They are not suitable for applications that require continuous throttling.
Check Valve/Non-return Valve
A check valve is used to prevent backflow in piping systems. The valve opens due to the pressure of the fluid passing through the pipeline. Reverse flow closes the valve and prevents the fluid from moving in the opposite direction. Check valves do not require external control. They work automatically and hence do not have an operating handle or stem. The simplest check valves are designed with a one-way flap mechanism.
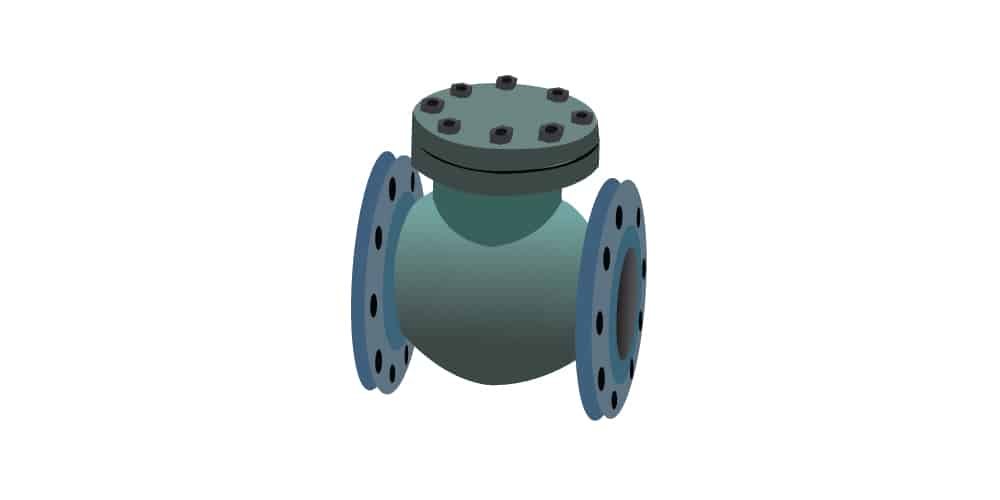
Check valves are generally small, simple, and inexpensive. Industrial applications of check valves include feed water control systems, gas systems that mix multiple gases into a single gas stream, and fuel and oxidizer mixing systems. In domestic applications check valves are often used to prevent mixing of a sanitary potable water supply with water from unsanitary systems.
Plug Valve
Plug valves use a cylindrical or conically tapered plug to allow or restrict fluid flow. The plug has one or more hollow passageways that allow the fluid to pass through when the passage is aligned with the flow direction. A quarter-turn rotary motion is required to turn the plug and block the fluid flow. Plug valves perform well in slurry applications. The wiping action of the plug does not allow suspended particles to accumulate and form an obstruction. Typical applications of plug valves include gaseous, and vapor services, natural gas piping systems, oil piping systems, coal, mineral and sewage applications. They are also suitable for vacuum and high-pressure applications.
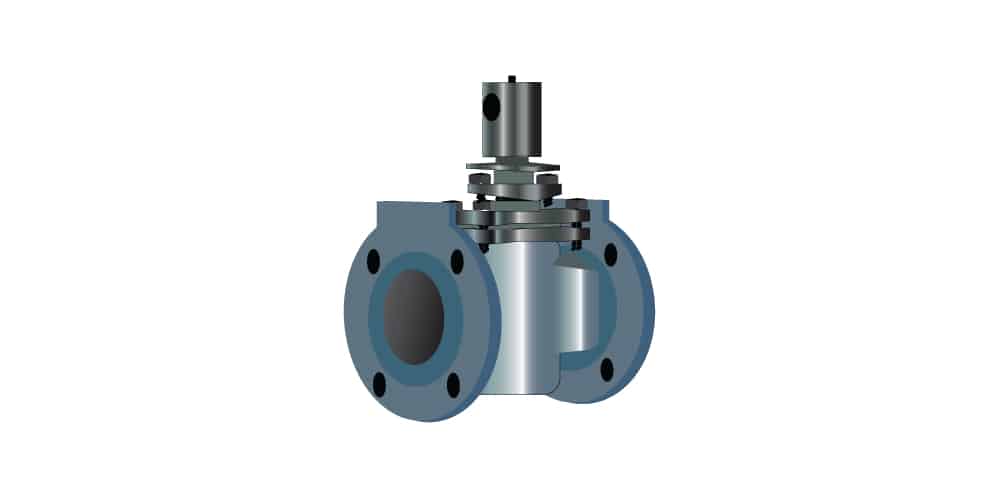
Plug valves offer a long service life and high reliability which makes them suitable for corrosive, abrasive, and toxic materials. They are usually used as on-off stop valves to provide quick bubble-tight shutoff. The valves can be repaired and cleaned without removal of the body from the piping system. Plug valves are not recommended for throttling applications and applications that require high frequency switching. Compared to ball valves, they cost more and require greater force to actuate, due to higher friction.
Butterfly Valve
The “butterfly” refers to a rotatable metal disc mounted on a rod. A quarter turn of the disc is required to open or shut-off the valve. In the closed position, the disk completely blocks off the passageway. In the open position, the face of the disc is parallel to the flow direction and allows nearly unrestricted fluid flow. Butterfly valves find applications in cooling water systems, compressed air or gas applications, fire protection, slurry services, vacuum service, and high-pressure / high-temperature water and steam services.

Butterfly valves have a short circular body which reduces space requirement and makes them light weight and easier to install. The compact design also makes them suitable for large valve applications. Butterfly valves have a high coefficient of flow. They offer good sealing even at low pressure. On the other hand, butterfly valves can be difficult to clean, and the throttling function is limited to low differential pressure and unguided disc movement can be affected by flow turbulence.
Needle Valve
Needle valves are similar in design to globe valves. The plugging element in these valves is a long, tapered, needle-like plunger which fits into a matching seat to stop the flow. A stem is turned to insert or retracted the plunger, opening or restricting the flow path. The finely-threaded stem requires many turns to fully retract the plunger; this feature allows precise regulation of the flow rate. Needle valves are typically used in small diameter piping systems where very fine control of flow is desired. Needle valves are generally suitable for systems with low viscosity fluids flowing at low flow rates. The most common application is to regulate flow to fragile gauges in order to protect them from damage caused by an abrupt pressure surge. They are also used as bleed valves to relieve pressure or to drain off the fluid for analysis or for maintenance.
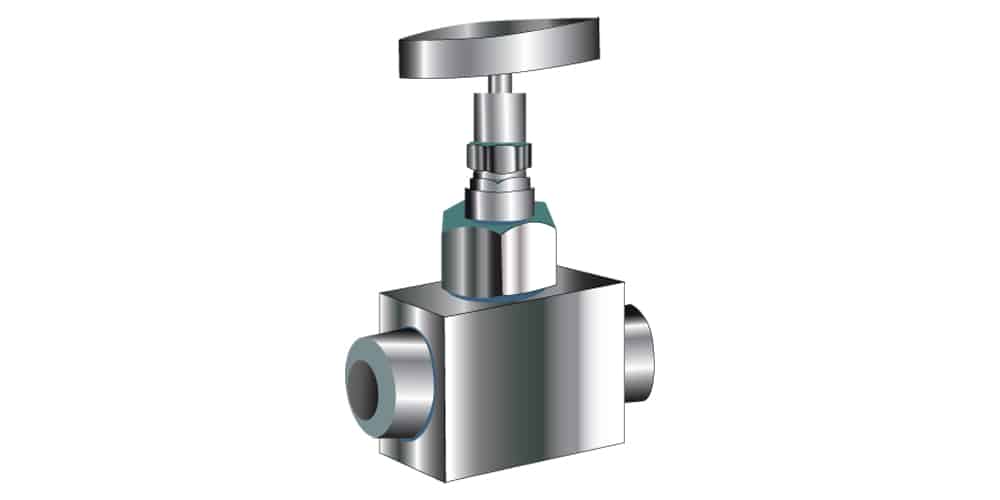
The valves are only suitable for low flow rates as the flow passage between the seat and the needle is small. Needle valves are not suitable for fluids with suspended solids. Use of excessive force during shut-off can damage the seat of the needle valve.
Pinch Valve
Pinch valves employ an elastic tubing and a pinching device that directly restricts the flow through the tubing. The pinching mechanism flattens the tubing to create a seal.
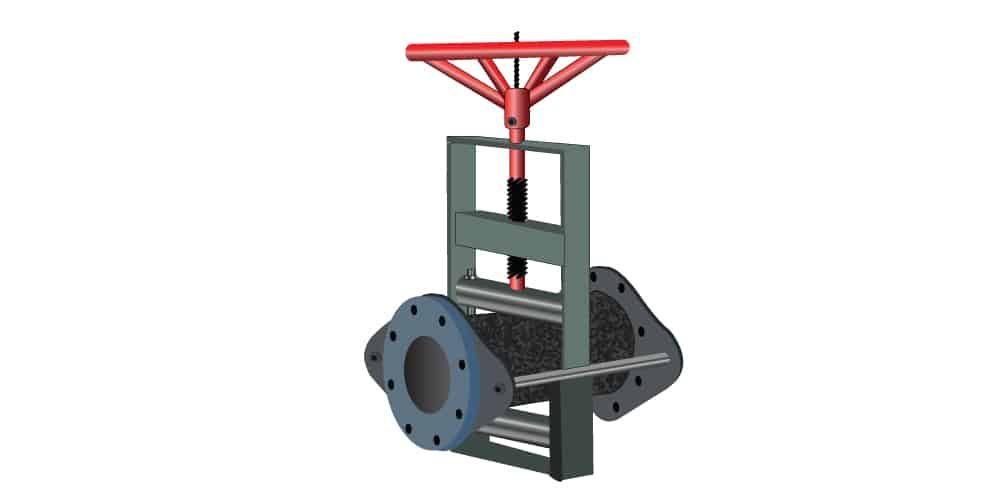
Pinch valves can be used to start, stop, and regulate fluid flow. Since these valves have fewer components, they are relatively cheaper and more leak-proof as compared to other valves. These valves are ideal for pneumatic conveying of solid materials and for handling of slurries. Pinch valves minimize turbulence and friction during flow. They are, however, not suitable for gases and for high-temperature or high-pressure applications. A high pressure-differential or vacuum in the system can cause the tubing to collapse or deform resulting in incomplete opening of the valve.
Diaphragm Valve
A diaphragm valve, also known as a membrane valve, consists of an elastomeric diaphragm, and a saddle/seat upon which the diaphragm closes. A linear compressor is used to push the thin, flexible diaphragm into contact with the seat/saddle to close the valve. Diaphragm valves also allow partial closure of the passageway making them suitable for throttling applications. They are suitable for viscous fluids and fluids containing solid materials as the solids are not trapped in the valve mechanism. Diaphragm valves are commonly used in water treatment facilities, pharmaceutical, food and chemical plants, vacuum services and corrosive applications.
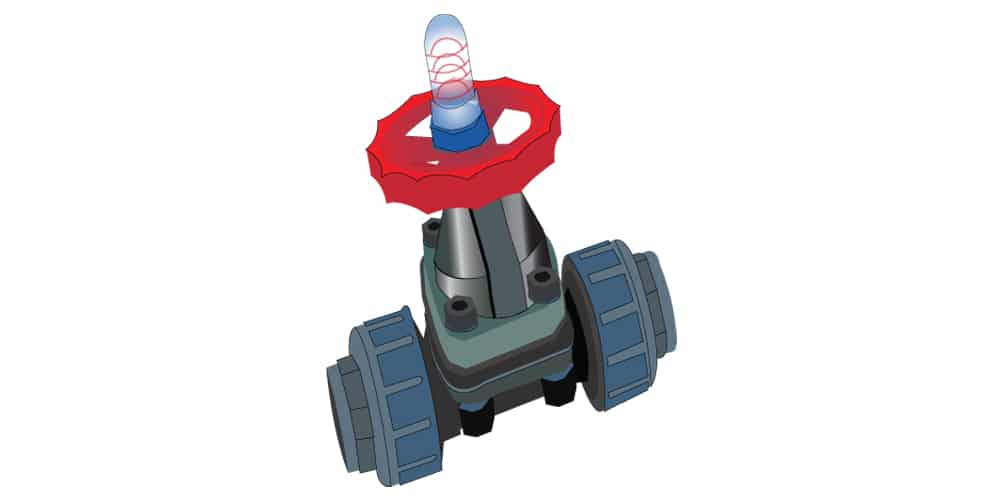
Diaphragm valves are leak-proof, easy to maintain, clean, safe, and effective. They are suitable for moderate pressure & temperature applications. The working temperature and pressures of diaphragm valves depend upon the diaphragm material. The saddle in a diaphragm valve can prevent complete drainage of the pipe. When used in continuous throttling applications, the diaphragm can wear out over time leading to valve failure.
How are valves in piping systems classified?
There are several different ways in which valves can be classified. They can be grouped based on their function, type of operating mechanism, end connections, mechanical motion, construction material, pressure and temperature ratings and port size. When choosing a valve, it is important to consider each of these classifications to ensure that the valve is suitable for the desired application.
( A ) Valve function
Valves are incorporated in a process to perform different functions. They may be used to start/stop the flow or to regulate flow and pressure. They may be required to control the direction of flow, or for improving process safety. Based on flow control, valves are classified as either isolation valves or regulation valves.
Isolation valves
Isolation valves are designed to either completely restrict fluid flow or allow it without obstruction. These valves are not recommended for continuous use in the partially open state as they may provide poor flow control or suffer wear damage over time.
Regulation valves
Regulation valves are used for regulation of pressure and fluid flow with suitable precision. These valves can be safely and efficiently used in processes that require partial open or closed state.
Some valves are suitable to perform both functions while others are recommended only for one. The table below classifies the valves discussed above according to their function.
Valve type | Isolation | Regulation |
---|---|---|
Gate valve | ||
Globe valve | ||
Ball valve | ||
Check valve / NRV | ||
Plug valve | ||
Butterfly valve | ||
Needle valve | ||
Pinch valve | ||
Diaphragm valve |
( B ) Mode of operation
Valves can be classified as manual, actuated or automatic based on how they are operated.
Manual valves
Manual valves are typically operated by hand with the help of wheels, levers, pedals, knobs, or chains. These valves can be geared mechanically to change the direction of movement and/or to increase the operation speed or torque.
Actuated valves
In high-precision or large-scale applications, valves are often connected to electric motors, pneumatic systems, hydraulic systems, or solenoids, to enable remote operation and automation of valve function.
- Electric motor actuators:Electric motor actuators use reversible electric motors to rotate the valve stem through a gear system that increases torque and reduces rotational speed.
- Pneumatic actuators:Pneumatic actuators use air pressure to provide the force needed to operate the valve.
- Hydraulic actuators:Hydraulic actuators use a pressurized liquid and a piston to deliver the force required to operate the valve.
- Solenoid actuators:Solenoid actuators employ the magnetic attraction between a slug attached to the valve stem and the coil of an electromagnet to operate the valve.
Automatic valves
Some valves are automatically activated when a specific flow condition is met. For examples, check valves close without any need for outside intervention during backflow. Similarly, pressure release valves are activated automatically when an over-pressure condition is detected.
( C ) End connections
Valves are connected to pipes through joints; these joints can be screwed, flanged or welded. Some common types of valve ends are listed below:
- Flanged end valves:A flange is a plate or ring that forms a rim at the end of a pipe or valve; two flanges are bolted together to form a joint.
- Screwed end valves:Screwed end valves have threaded joints, to which the end of a pipe or another fitting is screwed.
- Socket welded valves:The pipe is inserted into a socket and welded.
- Butt weld valve:The butt weld valves have beveled ends that match a similar bevel on the pipe.
- Wafer type valves:The thin valve body is placed between two pipe flanges, with the bolts surrounding the valve body. These valves are usually installed in systems with limited space.
( D ) Mechanical motion
Based on the mechanical motion of the closing element, valves can be classified as Linear Motion Valves or Rotary Motion Valves. If the closing element in the valve moves in a straight line to allow or stop the flow, the valve is called a linear motion valve. When the closing element rotates or moves along a circular path the valve is called a rotary motion valve.
Valves can also be classified as multi-turn or quarter turn depending on the extent of turning of the handle/wheel required to completely open or close the valve. Rotary motion valves often require only a quarter turn (90°) of the stem to go from fully open to a fully closed position.
The classification of some common types of valves, based on mechanical motion, is presented in the table below:
Valve type | Linear motion | Rotary motion | Quarter turn |
---|---|---|---|
Gate valve | |||
Globe valve | |||
Ball valve | |||
Check valve / NRV | |||
Plug valve | |||
Butterfly valve | |||
Pinch valve | |||
Diaphragm valve |
( E ) Construction material
The valve body can be made of stainless steel, alloy steel, brass, cast iron, or plastics depending on the desired temperature and pressure ratings, durability, and application. The gasket, packing, and valve seat are usually made of PTFE, POM, FKM, PA, EPDM, or NBR to achieve the desired level of seal and temperature/pressure ratings.
( F ) Pressure-temperature ratings
Valves may also be classified according to their pressure and temperature ratings. These ratings specify the maximum allowable pressure and temperature levels to which the valve may be safely subjected.
Conclusion
Valves are available in a large variety of designs and configurations. The large number of available options make valve selection a difficult task. Choosing the best valve for an application requires consideration of the required function, fluid service conditions and characteristics, frequency of operation, isolation or regulation requirements, maintenance needs, and the desired level of safety and reliability. Valve manufacturers can help you select the best valve for your application.
Image Source: © phojaip (Adobe Stock), tomas (Adobe Stock), matrivgraphics (Fiverr) & AS-Schneider