How a natural gas terminal meets 99% supply availability with DBB valves
The cease of natural gas imports from Russia forced Germany to switch from energy providers. Since then, Norway has grabbed the number one spot as the main supplier. To secure reliable gas transfer and distribution, all facilities within the circuit must be at peak capacity.
One of those facilities is a Gassco plant located in northern Germany. The revamped Emden natural gas terminal kicked off operations in 2016 with the operative premise of providing an availability delivery rate above 99%.
Since the start-up the plant did not reach its potential due to a leakage problem at the shut-off valves. Together with the customer, we set about working out a solution to achieve the high requirement of 99% availability. Here’s how we helped Gassco get to the promised target.
About the plant
Gassco’s natural gas terminal in Emden is part of a circuit built in northern Germany to receive Norwegian gas from the Northsea. Below, we present you with a brief description of the facility.
Facility type | Location | Heading #3 | Product |
---|---|---|---|
Natural gas terminal | Gassco | Emden, Germany | 1,300-gigawatt hours
of natural gas |
Brief facility description |
---|
The Northsea natural gas terminal was built in 1977 to receive the gas feed from the Norpipe. In 2016, the 60,000 m2 facility completed a refurbishing process meant to improve operations and enhance safety.
Upon arrival, the gas flow is metered and then sent to treatment in a hydrogen sulfide removal unit. Conditions such as pressure and temperature are regulated beforehand.
Once conditioned, the treated gas passes through quality control and metering checks before entering the transmission system. From there, it goes directly to the end user for downstream operations or temporary natural gas storage. |
Our mission with this project
During the commissioning phase of the natural gas terminal in Emden in 2016, various shut-off valves displayed leakage problems. At the time, several improvements were carried out to keep the plant operating at minimum reliable conditions. Unfortunately, in the long term, the problem persisted. And the previous valves delivered by another supplier continued leaking.
Gassco needed a partner in crime to find the right solution to their issues. They craved to regain peace of mind and perform according to their design premise—more than 99% availability delivery rate. So, in 2018, they reached out to AS-Schneider.
We excitedly took the chance to collaborate with them. It was a special opportunity to help out by recommending the most fitting solution for their application, securing a supply availability above 99%.
Our first course of action was to visit the facility to:
- Meet the head of maintenance and maintenance technicians;
- Gather information; and
- Inspect the valves, of course!
At the first visit, we couldn’t help but strongly suspect that Emden’s team was subject to incorrect advice on product selection. Thus, our efforts centered on solving the issue by finding the right fit for their specific purpose – reliable DBB Valves that are precisely matched to the application.
A request is sent to solve the valve leakage issues and secure trouble-free operations
When Gassco’s mechanical coordinator, Axel van der Berg, first approached us, his remarks were crystal clear about the areas of improvement they sought to enhance. In short words, the plant needed a DBB Valve solution that would:
- Enable safer operations;
- Promote the well-being of their people, the environment, and the plant;
- Ensure a reliable natural gas supply—even in winter; and
- Guarantee a supply availability above 99%.
The valves had to meet these technical specifications:
- Zero leakage. No leakage to the outside. Total tightness in the seal at the termination.
- Able to withstand harsh environments. The natural gas receiving terminal is located by the Northsea coast, in Rysumer Nacken—a region infused with salty air prone to cause corrosion.
- Fit for high-high pressure and temperature conditions. The more gas withdrawals there are in the gas transport system, the lower the pipeline pressure is. To prevent stalls, the natural gas is compressed to ~ 100 bar.
The ball was suddenly in our court. It was time to respond and get our hands dirty!
Customized DBB valve solution for the respective challenge
After listening to the details our customer kindly shared, we went home to work on a solution that catered to fix each concern.
We started by assessing the issue more thoroughly. We went over the valve design factors and studied the facility’s operating conditions in and around the shut-off valves with leakage issues. As it turns out, our first hunch was correct. The root cause resided in the poor selection of valves for the particular application.
The next step to follow was to adapt our DBB Valve to meet Gassco’s requirements. Afterward, we presented two solutions:
#1. VariAS-Blocks with DBB floating ball design
Here’s a single-unit solution designed to succeed the traditional, multiple-valve installations. In our configuration, the primary shut-off is designed as a process valve. Mechanically, they are flanged directly to the “main” process line, forming an interface between the process itself and the measuring device. The primary and secondary isolation valves are standard ball types with floating balls. The bleed valve regularly is a ball type as well but could also be a needle valve with a screwed bonnet. This arrangement enables isolation on both ends. The bleed is there to allow venting of the device’s cavities during maintenance.
For the project’s purpose, we had to redesign our own product so it could work bi-directionally. The adjustment consisted of repurposing the relief hole of the inner ball. Instead of just pointing vertically upwards below the packing, it could also point into the downstream side. This small but meaningful modification allows relief on the upstream and downstream sides alike. It will all depend on which side is receiving the higher pressure.
#2. Double block & bleed piping ball valves (Taurus Series)
Our Taurus Series features a twin-ball design that suits many applications in the oil and gas industry. The compact configuration enables the incorporation of a floating ball or trunnion-mounted arrangement in the primary and secondary isolation valves. The bleed valve can be provided as an integral needle type valve with a screwed or flanged bonnet or as a flanged valve (ball type, VariAS-Block, or Monoflange).
These pictures show a closer look at the products selected, without the actuators.
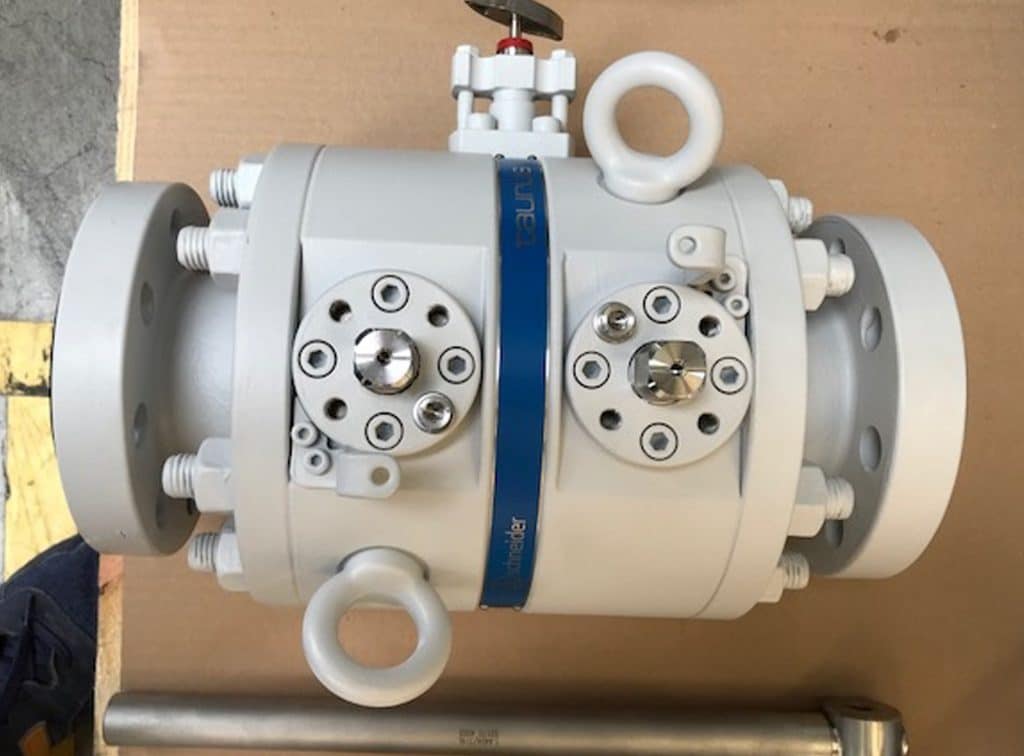
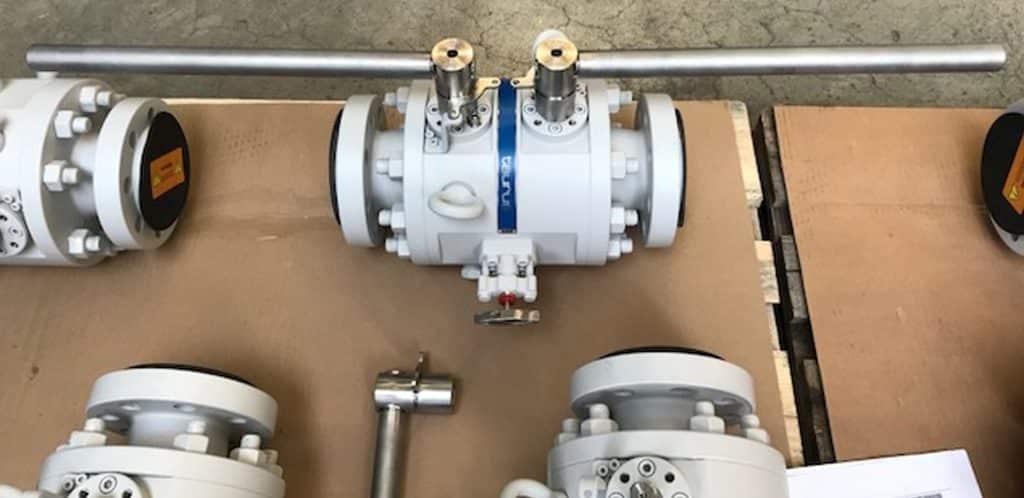
Then came the time to prepare for the installation phase. We had rushed expectations to see if the VariAS-Block with a floating ball design would respond as well in the field as it did in our shop. If so, along with the Taurus Series’ solutions, they would allow the Northsea natural gas terminal to operate without concerns of a shut-off valve leakage. And in return, they will meet the targets of:
Enhanced safety and reliability in the operations while reclaiming the 99%+ supply availability.
Replacing faulty valves with the right products
The shut-off valve arrangement in the Northsea natural gas terminal has a bypass application like the one shown in the sketch below. A combination of the VariAS-Block with DBB floating ball design and the Taurus Series’ double block & bleed piping ball valves was in the cards.
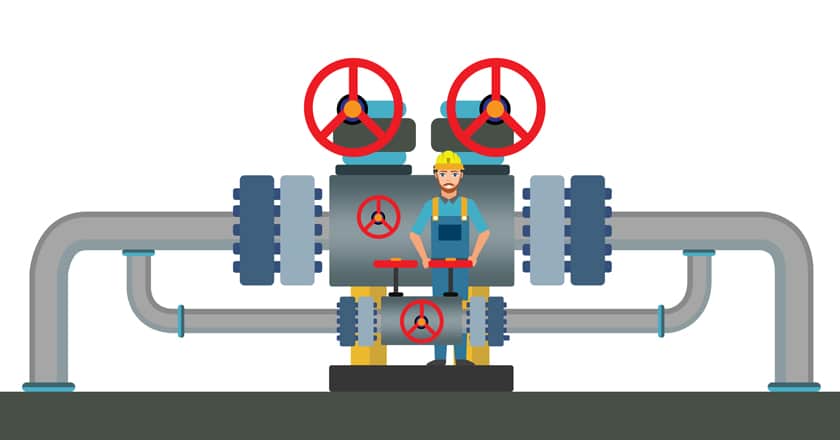
We began the bypass installation in 2019. That’s when the leaking/bad valves from the previous supplier were discarded by our reliable DBB valves.
Due to budget restrictions, only the valves that posed a direct risk to human and environmental safety were replaced in 2019. The remaining were successfully substituted during a planned shutdown of the facility scheduled in 2022.
And guess what? The VariAS-Block with DBB floating ball design passed the test with flying colors. As did the Taurus Series devices selected.
What to consider when selecting a valve
Valves are flow control devices that not only change in type and size. They also have particular design mechanisms adapted to fit a given application.
For example, in a process with flushing operations:
- The valve must be tight from the inside to the outside during normal conditions.
- But while flushing, the same valve must be able to let in flow from the outer rinsing medium into the system by means of applied pressure in the same direction—from the outside to the inside.
To meet both process requirements, the selection of a bidirectional valve design is inevitable.
For the Northsea natural gas terminal, such consideration went under the rug. Ergo, only unidirectional valves were considered and installed by our competitor.
The unfitting valve selection drove the recurrent leakage issues that caused:
- Safety concerns for operators, the surroundings, the environment, and the facility itself.
- Operational unreliability and process disruption.
- Higher OPEX, as the leaking valves had to be replaced constantly (total costs of ownership).
- Delivery rates below the targeted 99%.
Our first advice to operators is to ensure manufacturers comprehend the processes carried forward. Otherwise, their technology selection might fail. The second one is for them to work with experts in the field. Real pros will care about their operations and won’t be hesitant to cover the aspects necessary to secure the delivery of a lasting and reliable product.
Outro
The Gassco project introduced a thrilling opportunity for the AS-Scheider family. Adding a grain of sand to return the revamped Northsea natural gas terminal to top form amid today’s energy climate.
We are glad to see that our modified VariAS-Block (with a piping ball) design and the double block and bleed piping ball Taurus Series products did their part, assisting the wonderful team at Emden. After years of battling with shut-off valve leakage issues caused by the poor technology selection of a competitor of ours, they can now finally say the plant is:
- Operating at peak safety conditions.
- Ensuring a reliable natural gas supply; and
- Guaranteeing a supply availability above 99%.
Moments like this make us proud to do what we do. Being a trusted partner that operators can turn to to overcome pressing worries is one of our greatest joys.
Image Source: © fotowunsch (Adobe Stock), Zuhaibnaqvi (Fiverr) & AS-Schneider