Flow control operations: Floating vs. trunnion-mounted ball valves
Every engineer encounters the challenge of having to choose one technology over another. A notable example is specifying the valve solution for a given process line. Sometimes the choice is evident. Other times, it is a tight horse race of options.
In light of that, in this article, I want to focus on a topic I frequently get asked about: the differences between floating and trunnion-mounted ball valves. Selecting the most valve of the two for a specific service could be tricky at times. Thus, knowing what sets them apart helps a long way. Read on to learn about both valve solutions. My goal is to lead you to identify which design is more appropriate.
Ball valves are widely used for a reason. Here’s what makes them stand out
Ball valves are reliable and durable flow regulation devices. They work with an on/off control activated by means of a centered bored (and holed) rotary ball that changes position against applied pressure. The simple yet functional design comprises these main parts:
- shell or body;
- rotary ball with a port;
- trim section (stem, seats or seal rings, disk, sleeves);
- bonnets;
- packing; and
- handle, levers or gears for manual operation or an actuated power source (pneumatic, hydraulic, electric) for automatized operations.
Material-wise, the ball is usually made of steel, while the seats are fabricated from polymers like PTFE or metals.
In spite of some limitations in the throttling capacity, ball valves are well-suited for many industrial-level applications in oil & gas, petrochemical, energy, water, and manufacturing facilities. The compactness of the piece favors fast response times and low maintenance requirements.
When the valve switches to the open position, the ball rotates 90 degrees to align the port with the body. This mechanism lets the medium pass through. In the closed position, the ball must retreat those 90 degrees to seal the medium against its pressure. In a tight shut-off, the sealing elements must be pressed together by preloading the seats. The system’s pressure is also a contributing factor. The higher the pressure, the higher the force needed to push the sealing elements together.
Ball valves in high-pressure applications
When a line’s pressure is on the rise, the sealing elements of the ball valve are more tightly pressed together. In parallel, the ball and seat are subject to stronger forces. This scenario would not represent an issue for a device like a check valve. However, in ball valves, it could bring serious trouble. Why? Because they are central process fixtures that must remain operable, even amid a high differential pressure condition.
For valves, a high-pressure setting is synonymous with high operating torque and a larger manual effort. So, when designers work within a high-pressure range, they may end up with calculations for lengthy handles and expensive gear requirements. Appropriately enough, the handle’s design can be bound by standards such as ISO14313 and API 6D. Both provide rules on how to prevent collisions with other piping elements.
One way to decrease the operating torque is by reducing the friction coefficient of the material pair, i.e., using modified plastics (PTFE-filled PEEK). Though the results are not always as majorly significant as needed.
Another option is to assess other valve components and take action from the findings. As an idea, look at the stem. Big stem diameters increase the size of the valve’s body, raising operating torque (and costs).
The target is to analyze all measures that add protection to the sealing elements. And the effective way to do it is by lowering the operating torque and impact forces. Both are critical to extending the valve’s lifespan, especially in high-pressure conditions.
That’s why knowing the types of ball valves is decisive in getting the design right.
Types of ball valve
Floating ball valves
They are considered versatile, economical, and the most popular type of ball valves. The name can be attributed to their working mechanism in which the ball ‘floats’ between two seats located upstream and downstream. This is made possible by a design configuration that connects the ball to the body directly through the seats, meaning there is no structure to support it while it is suspended in the medium.
Floating ball valves come in various body types (one-piece, two-piece, and three-piece).
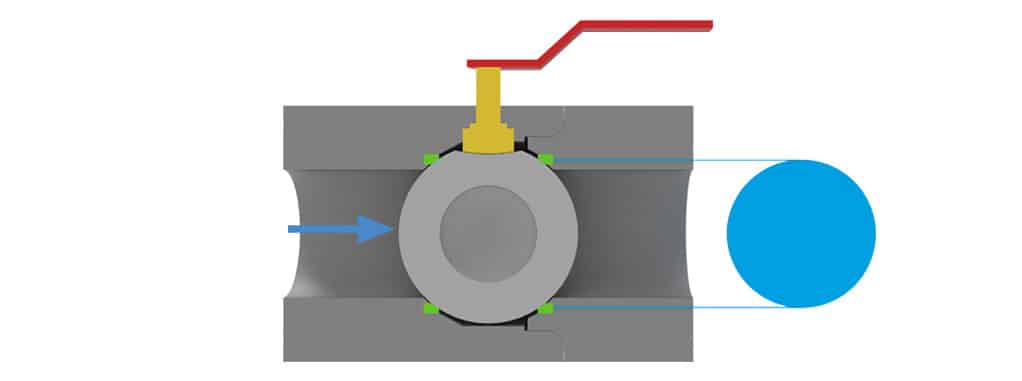
Trunnion-mounted ball valves
Unlike the floating counterpart, trunnion-mounted ball valves do come with a support structure that constrains the ball while the flow regulation takes place in the pipeline. The movement restriction is done by means of a bearing retained in the stem and a second trunnion located opposite the stem. This arrangement makes it the most expensive ball valve solution of the two.
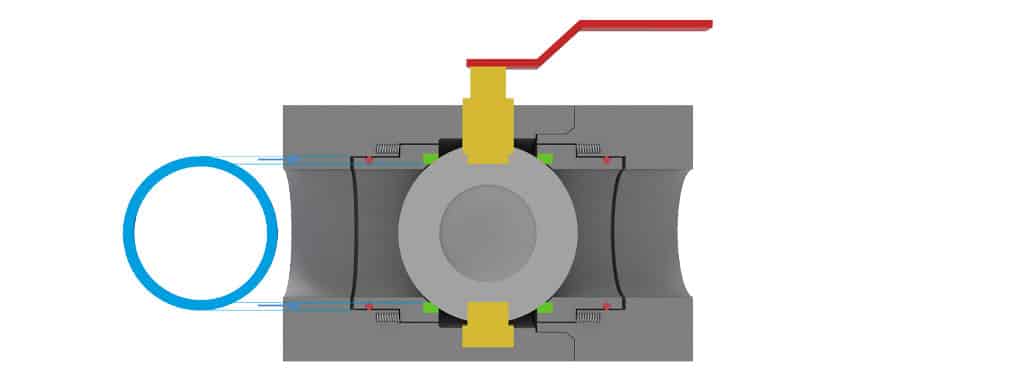
What ball valve is the right fit for your process? Floating or trunnion-mounted?
As previously stated, reducing the operating torque and forces on the sealing elements is a defining factor in ball valve design. The stances get even bigger in high-pressure applications.
So, how do you approach this challenge?
#1 One way is to revisit the formula used to calculate the force applied to the sealing elements.
F
O
R
M
U
L
A
F = p x A
F = Force
p = pressure
A = Area on which the pressure is applied
F
O
R
M
U
L
A
As seen above, the force depends on the pressure and area. Since the pressure is a given, the best choice to lower the force is by decreasing the size of the area. Following this logic, the trunnion-mounted design has the upper hand in ensuring:
- lower operating torque; and
- less wear on the seats
If so, how are floating ball valves the most popular of the two?
That would be because trunnion valves have more components; hence, they are far more expensive.
#2 What other criteria are available?
Standard EEMUA 182 gives clear rules on when to use the trunnion ball design:
- class 150 to 300, DN 150 (NPS 6), and higher
- class 600 to 2500, DN 50 (NPS 2), and higher.
My opinion
For small bore sizes, there is no need for a trunnion ball. Consider a trunnion starting with class 600.
Moreover, I also only see one scenario where both valves comply. The DN50 (NPS 2) size. Still, when in doubt, trust the valve manufacturer. It’s within his responsibilities to test the different pressure classes and bore size combinations before setting on the valve’s design basis.
For more context, you can consult the AS-Schneider product catalog. It offers:
FLOATING
BALL DESIGN
TRUNNION-MOUNTED BALL DESIGN
DN 25 (NPS 1) up to
DN 50 (NPS 2)
DN 50 (NPS 2) and
bigger
The most important things about floating and trunnion-mounted ball valves in summary
- Ball valves are suitable for several industries, including oil and gas, petrochemical, and energy. Their design is reliable, lasting, affordable, and easy to maintain.
- When designing a ball valve, keep the operating torque and applied forces on the sealing elements to a minimum matter. Especially in high-pressure conditions. Otherwise, performance and longevity will be compromised.
- There are two types of ball valves, floating and trunnion-mounted. They are similar in functionality but slightly different in design. In the first, the rotary ball is only connected to the seats. In the latter, it is held in the body with a trunnion.
- Floating ball valves are the most used of the two. Trunnion-mounted valves are specified when larger pipeline sizes and high-pressure conditions are involved (class 600 and above).
- Knowing the key differences between the floating and trunnion-mounted designs is essential to meet process, budget, performance, and maintenance targets.
Image Source: © pichitstocker (Adobe Stock), Vulong87 (Fiverr) & AS-Schneider