New chemical plant complies with the stricter TA-Luft amendment in the field of valves
The amended Technical Instructions on Air Quality Control (TA-Luft) regulation came into effect on December 1, 2021. The updated regulation specifies stricter new limits for fugitive emissions from chemical plants. This is a tough challenge for the chemical industry.
In my article, I describe a case study of the challenge engineers faced in selecting compliant valves when building a new chemical plant in Germany.
Amendment of TA-Luft Regulation
Originally introduced in 1964, the Technical Instructions on Air Quality Control, (TA-Luft) serves to protect the general public from the harmful effects of air pollution on the environment. The regulation has been revised several times to address increasing environmental concerns.
The German government has recently published a new edition of the TA-Luft which came into force on December 1, 2021. The latest amendments are intended to realign the outdated regulations with the requirements in EU regulations.
In order to achieve a higher level of protection for the environment, the latest version of TA-Luft specifies more stringent limits for pollutants emitted by facilities that require emission control permits.
The major change in terms of valve specifications is the adoption of the ISO 15848-1 standard in place of the VDI 2440. The ISO 15848-1 standard precisely regulates the test process and test conditions. So that every manufacturer is required to test their valves in the same way.
For further details regarding the amended TA-Luft, please refer to this earlier article on the Impact of revision of the TA-Luft on the valve industry. The article was written by my colleague Markus Häffner. He is a member of the corresponding TA-Luft working group, he describes there many valuable details.
In view of the new TA-Luft regulation, existing installations need to upgrade their valves to comply with ISO 15848-1 specifications.
New facilities that are currently at the planning or installation stage must choose valves that comply with these specifications.
Project description of the chemical plant
INEOS Phenol is the largest producer of Acetone and Phenol in the world. The company is building a new, state of the art Cumene plant. It covers an area of 16,000 square meters in the Marl Chemical Park in North Rhine-Westphalia, Germany.
Cumene is an aromatic hydrocarbon used as an intermediate for the production of Acetone and Phenol.
The production facility has been designed to produce more than 2,000 tons of Cumene per day. And it has an annual production capacity of 750,000 tons.
The new plant is being built to replace an older plant in Marl with design objectives of lower energy use. The plant should enable a higher production yield & a more environment-friendly production process.
The fully integrated plant will use existing pipeline links between INEOS’ Acetone and Phenol production plants in Gladbeck, the Marl Chemical Park and the BP refinery and cracker complex in Gelsenkirchen.
The pipeline integration is meant to support future demand. It is also intended to improve the security of supply of the INEOS plants in Gladbeck and Antwerp.
The need for a secure supply of Cumene, for the main Gladbeck plant was felt some years ago. Large quantities of raw material could not be transported to the plant because of the low water level of the Rhine. And deliveries by ship came to a standstill.
The plant including the new supply chain via the pipeline is expected to be commissioned during 2022.
Challenge for engineers to comply with the TA-Luft amendment
Environmental protection
The new INEOS plant is located near residential areas. Here, safety is a particularly high priority.
To meet its responsibility for the environment, INEOS has very strict in-house environmental and safety regulations. The purpose of these regulations is to protect the general public and the neighborhood. That preventive measures should help against harmful environmental effects caused by air pollution. And thus achieve a high level of protection for the environment as a whole.
In addition, the new Cumol project had to legally comply with the amended TA-Luft 2021, over the entire application area. As already mentioned, the amended TA-Luft refers to ISO 15848-1 for control of fugitive emissions released from valves. And that amendment includes much stricter limits for pollutants emitted from equipment that requires an emission control permit. This was a challenging issue for the company.
Valve requirements
The plant design required installation of compliant close-coupled valves with block and bleed or double block and bleed functionality at each pressure measuring point.
The specification for these valves, in terms of pressure, was not unusually high.
However, the temperature ranges can reach a huge span from -48°C to 320°C with this new Cumol plant. And this high temperature range was an appealing challenge for our engineers.
In the summer of 2020, INEOS entered into preliminary discussions with AS-Schneider. Together, we aimed to find a cost-efficient solution to this issue.
Solution to comply with the TA-Luft amendment
AS-Schneider already had valves in its range that complied with the TA-Luft 2002 requirements. That valves covered a temperature range from -30°C to +200°C, too. Additionally, that valves had been thoroughly tested over several years. They offered reliable and environmentally friendly performance but in a narrower temperature range.
It was possible for our engineers to extend the temperature range above 200°C using bellows to protect the upper parts. So that the existing valves could be used up to 550°C. The disadvantage of this approach is the additional cost, which makes the valve twice as expensive.
However, INEOS needed a cost-effective solution to its challenge. Thus, this was not a suitable solution for us. Our engineers were now faced with the task of developing a new packing for a TA-Luft 2021 compliant valve in a very short time.
After an internal workshop, the engineers identified a high temperature resistant packing suitable for this purpose.
The next hurdle was to meet the high tightness requirements over the entire temperature range. Since the TA-Luft was under revision at the time, and the proposed regulation hadn`t yet been finally adopted, we decided to fully comply with the ISO 15848-1 fugitive emission standard right away.
By December, we had developed a product that could pass the TA-Luft 2021 internal tests and was externally certified by TÜV Süd.
The newly developed valves meet the TA-Luft/ISO 15848-1 requirements. The valves are rated for a temperature range of −50°C to 400°C at a nominal pressure of up to 420bar with only one special packing.
We already supplied over 600 units of that range of Instrument Monoflanges with the new packing which covers temperature range of −50°C to 400°C to the chemical plant.
All Instrument Monoflanges complies with the stricter TA-Luft amendment (ISO 15848-1 fugitive emission standard) in the field of valves.
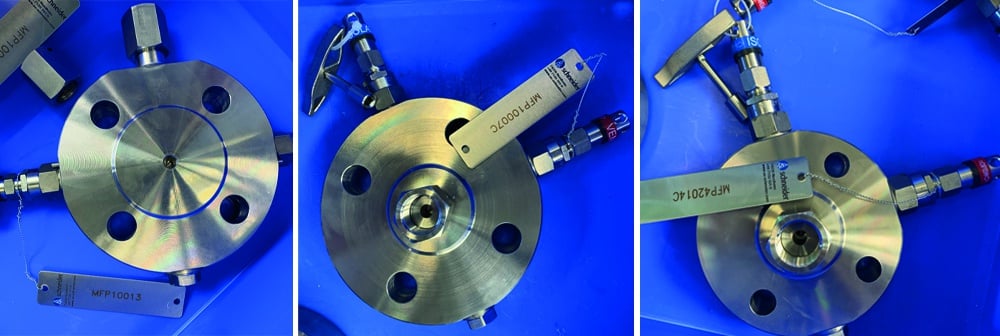
To avoid long waiting times at the testing laboratories, I recommend plant operators to choose valves that are certified for the new requirements of the TA-Luft amendment.
Stefan Heine, Sales Engineer at AS-Schneider Tweet
Conclusion
The amended TA-Luft regulation is expected to affect more than 50,000 facilities. And will affect industries like chemicals, metal production, waste treatment and food manufacturing. According to conservative estimates in the draft TA-Luft, compliance costs for industry are expected to exceed €691 million.
To meet the requirements set out in the TA-Luft amendment, plant operators urgently need to replace installed valves with valves that have been certified to comply with ISO 15848-1 requirements.
Our valves already comply with the TA-Luft amendment. The new valves are already being used safely in practice. Like at the above-described new chemical plant built by INEOS.
Image Source: © malp (Adobe Stock) & AS-Schneider