Challenge of Design Verification Test (DVT/TAT)
In my professional career I have found that in practice there is often misinterpretation in understanding Design Verification Test (DVT). DVT is formerly known as TAT (Type Acceptance Test) – a Shell Specification (MESC SPE 77/300A).
In the industry, there are many different manufacturers offering valves meeting Shell requirements. Users should also find out if these valves also meet the full Shell MESC SPE 77/300A Specification. This misinterpretation made me write this post.
Understanding Shell’s DVT/TAT (MESC SPE 77/300A)
The new term DVT is rarely used in practice. People still use the previous term TAT. That`s why I use in my post both terms.
When speaking about testing we also have to differentiate between that two terms:
1. Factory Acceptance Test (FAT)
The Factory Acceptance Test (FAT) assesses equipment during and after assembly. It confirms that the manufacturers have indeed built it. The FAT also ensures that users are operating it according to design specifications. Manufacturers conduct FATs to check non-conformities and inconsistencies, and to develop a procedure for managing these.
2. Design Verification Test (DVT/TAT)
DVT/TAT is a term used in Shell specifications, but it also appears in other standards besides Shell.
Performing a DVT/TAT test on a product already needs to be considered in design stage during developing the prototype.
The goal of a Design Verification Test is to ensure that a product meets all its design specifications. The DVT/TAT proves also if the valve design meets specific users` requirements or specifications. For example the Original Equipment Manufacturer (OEM) specifies a P/T rating. The DVT/TAT procedure proves or disproves this rating by performing a series of clearly defined mechanical and thermal cycles over the full range of the test valve temperature rating.
DVT/TAT increases customers’ trust in the reliability of a product. It is also useful for finding problems early. DVT/TAT reduces the likelihood of having to do an expensive fix later on, too.
General features of a DVT/TAT test
In the petrochemical industry, DVT/TAT involves the testing of valves. Engineers test these valves to their design limits on pressure and temperature (ambient temperature, elevated and minimum temperature). The procedure includes both: Several seat tests with use of nitrogen as well as body tests (static and dynamic) with use of helium to ensure tightness acc. Fugitive Emission Testing.
Engineers perform as many as about 200 mechanical cycles including opening and closing torques. The specification bases the acceptance criteria for required seat tests on ISO 5208 and values for shell/ body tests on ISO 15848 (FE).
DVT/TAT is part of a total valve qualification program:
- Technical documentation review
- Valve manufacturer technical audit (ISO 9001 methodology)
- Valve design validation and verification
How to approve a DVT/TAT test?
1) TAMAP = Technically Accepted Manufacturers and Products
Shell has a vendor management program known as TAMAP, which is a very extensive and multi-annual testing procedure. Vendors must undergo detailed product quality reviews. They also do a thorough screening of their quality assurance and control procedures. TAMAP assesses the capability of valve manufacturers. It ensures that they prove the full functional performance of their industrial valves.
The participation of Shell executives guarantees the standard of the reviews conducted. They challenge each phase of the supply chain. When valves have passed the TAMAP, they receive a certificate of acceptance. This certificate is valid for five years. Shell then adds the tested valve types to the TAMAP database.
Negative aspects:
- Very cost and time intensive testing procedure.
- Not common in practice.
- Shell adds the tested valve and also those which are included according valve qualification range to the TAMAP database. Any valve out of this clearly defined range which is different, but obviously similar, need to undergo the whole approval process again.
2) Third party testing e.g. with the German TÜV Süd
More common in practice is the testing procedure with a third party like TÜV Süd. It is not as extensive as the procedure to be approved for TAMAP database, and it also does not take a long time since the manufacture has a working design to pass all required tests. However, I don`t think it is not as safe or as professional as a TAMAP listed one as the technical procedure and conditions are identical.
Shell MESC SPE 77/300 – Valves class & size qualification range
Below you can find first table (valves DN50 and smaller) of qualification range by Shell MESC SPE 77/300 Standard. Qualification range describes the range of valves – considering pressure class and bore diameter – which are automatically qualified even no further tests have been performed.
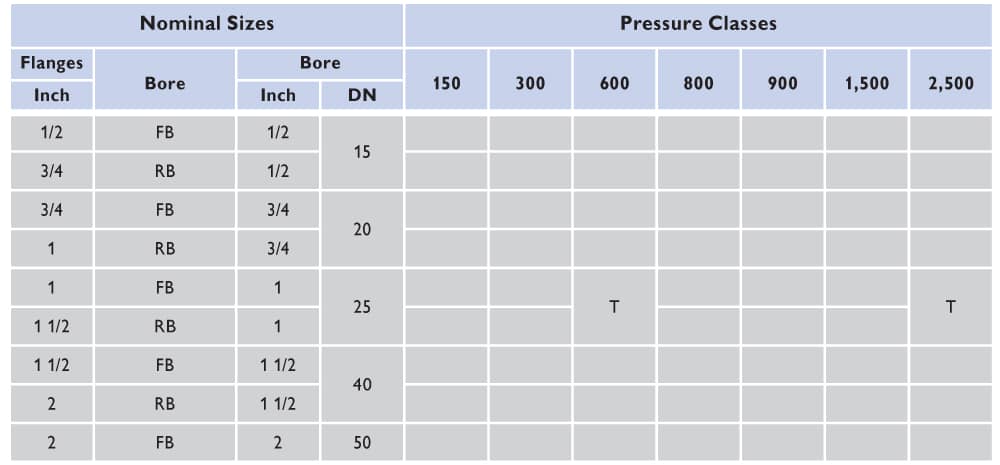
Info Box
The challenge of a DVT/TAT test
Designing and preparation of a product range to undergo DVT/TAT can be very challenging. It’s always a defined testing procedure. (Shell tests, seat tests, FE tests static and also dynamic). It follows specified factors. These factors include the testing temperature at ambient, elevated, low, or even cryogenic levels – depends on the design conditions of the valve itself. Acceptance criteria are also given in MESC SPE 77/300A. The primary aim of a Shell TAT is to show the customer that any possible change of temperature or pressure does not effect negatively on valve tightness. Therefore the very special combination of shell tests, seat tightness tests as well as fugitive emission tests are getting performed determining also any potential leak paths to the atmosphere.
Beware of misinterpreted DVT/TAT tested valves
In the industry, there are many different manufacturers offering valves meeting Shell TAT requirements. However, users should also be aware if they meet the full specification.
Example:
A ball valve with a design temperature -50°C up to 150°C is inquired by customer. TAT is also one requirement.
The whole TAT procedure must be based on this temperature range, means the manufacturer needs to perform the whole procedure at every temperature range:
- Ambient temperature
- Max. temperature à 150°C
- Low temperature intermediate à -29°C
- Min. temperature à -50°C
The most common deviation of manufacturers will surely be testing only from ambient temperature up to 150° – instead, the tests should be performed on the specified full range -50° to +150°.
Another common deviation is performing not the whole test procedure clearly given in MESC SPE 77/300 – often customers don’t exactly know this procedure. They expect to get a TAT approved valve but the valve has not went through the whole procedure.
In most cases, the lower temperature tests are more difficult to pass during a TAT procedure. You know why?
Melvin Tan
A valve obviously consists of many different single parts made of different materials, e.g. metal parts, graphite rings, soft seat inserts like PEEK or PTFE and other seals are typically used in valves.
All these materials have different physical coefficients of linear expansion. This difference always affects negatively on tightness of a valve – especially at lower temperatures.
Thus, the design needs to be able to compensate these different coefficients.
Our technical valve experts have gained experience in many areas. For example, they already know the potential leak paths of a typical valve. This knowledge is necessary for designing a valve that can meet stringent specifications and fulfill a range of heavy stress tests like DVT or TAT according MESC SPE 77/300 definitely is.