Are close-coupled installations the secret ingredient for painless measuring and improved TCO?
Am I building the plant my client wants? What needs to be done to make it so?As a plant builder, you have probably asked yourself those questions too many times. Even more, you sure know the answers. They imply technical assurance under the project’s budget and schedule constraints.
Regardless of how broad your expertise level might be, that’s never an easy cocktail to balance.
Throughout my career as an instrumentation hardware specialist, I have observed a significant trend among EPC engineers, particularly in the chemical industry. When choosing accessories for a measurement system, they tend to prioritize investment savings over the total cost of ownership (TOC). Even when those savings don’t guarantee smooth upkeep for the facility.
Under that umbrella, I want to introduce the value of a close-coupled installation as an extensive measurement solution for process plants.
After reading this blog, your next EPC project will aim to get the most out of this handy technology for your client’s delight.
What is a close-coupled installation? How is it different from a conventional setting?
A close-coupled installation is a mechanical configuration used to connect measuring devices to the process line with as less as possible interfaces.
Unlike in a conventional installation, impulse lines are no longer necessary to hook up the sensing devices or transmitters. Thus, eliminating extra causes of measurement errors, pressure drops, and other shady maintenance issues.
A close-coupled setting is suitable for most of industrial measuring applications. Yet, most plant builders stick to standard installations, thinking they might be a safer bet for everyone.
The operational reality, on the other hand, begs to differ.
Here are some reasons why.
Operational setbacks created by a conventional measurement installation
We had a client who was putting great effort into maintaining the conventional installation of a core unit. Those readings were paramount to securing product quality. Reliability was critical.
In a plan to ensure accuracy, they calibrated transmitters regularly and aimed to keep the impulse lines unclogged and uncorroded. The answer? More issues unfolded.
Vibration and leakage problems in the impulse piping started. Friction and temperature changes disrupted control and monitoring operations, creating errors in pressure and flow measurements. Product contamination became a constant threat.
Our client was desperate for a solution.
Close-coupled installations remove the never-ending impulse piping problems
When AS-Schneider was called for assistance, we did a careful assessment of our client’s situation. At that time, they were also facing pressure drop incidents caused by long distances to get to the measuring devices.
Project teams in an EPC devise strategies to cross the finish line on time and without breaking the bank. Going with standard installation becomes second nature at this point. Because of that, explaining to our clients which applications are better suited for standard installations and close couplings is always a priority for us.
As we were pitching to our client the idea to think about a re-design and to consider close-coupled installations, these benefits created the most excitement for them:
- Compact, self-contained design for the elimination of vibrations and unnecessary long distances to the measurement device.
- Plug-and-play configuration for a simplified process connection between elements (i.e., line, ball valve, and pressure instruments),
- Pre-assembly and pre-testing before site delivery,
- Savings in process pipework.
They overwhelmingly accepted close-coupled installations as a new kind of measuring for their plant. At last, it was time to say goodbye to fugitive emissions, vibration, hundreds of handles & needed maintenance observation walks and the other frustrating mishaps that made their shifts tedious and challenging.
From this experience, I can only advise EPC engineers to do the following before committing to a standard configuration at the start of a project:
- Ask operators about current maintenance needs,
- Talk to an expert about your concerns, or even better,
- Visit a plant site to see if the whole system works as intended and how it has held up over time.
Taking these steps will be formative and might lead you to reassess your approach to choosing the right solution for your project.
Instrumentation hardware in a close-coupled installation
Close-coupled installations are instrument mounting products built to bring the field instrument closer to the process. The combination of elements in a setup is referred to as instrumentation hardware. The close-coupled instrumentation hardware enables a direct and compact mounting process for the instrument.
Close-coupled instrumentation hardware is available for different types of instruments. The hook-ups include a combination of valves, manifolds, piping components, gaskets, bolts, special products, and flush rings.
In the pre-assembly and installation procedures:
- Valves, manifolds, and pressure instruments are directly connected to the process pipework.
- The process connection can vary between a flange, weld connection, or thread.
- The hardware is “hooked-up” to the process pipe on-site.
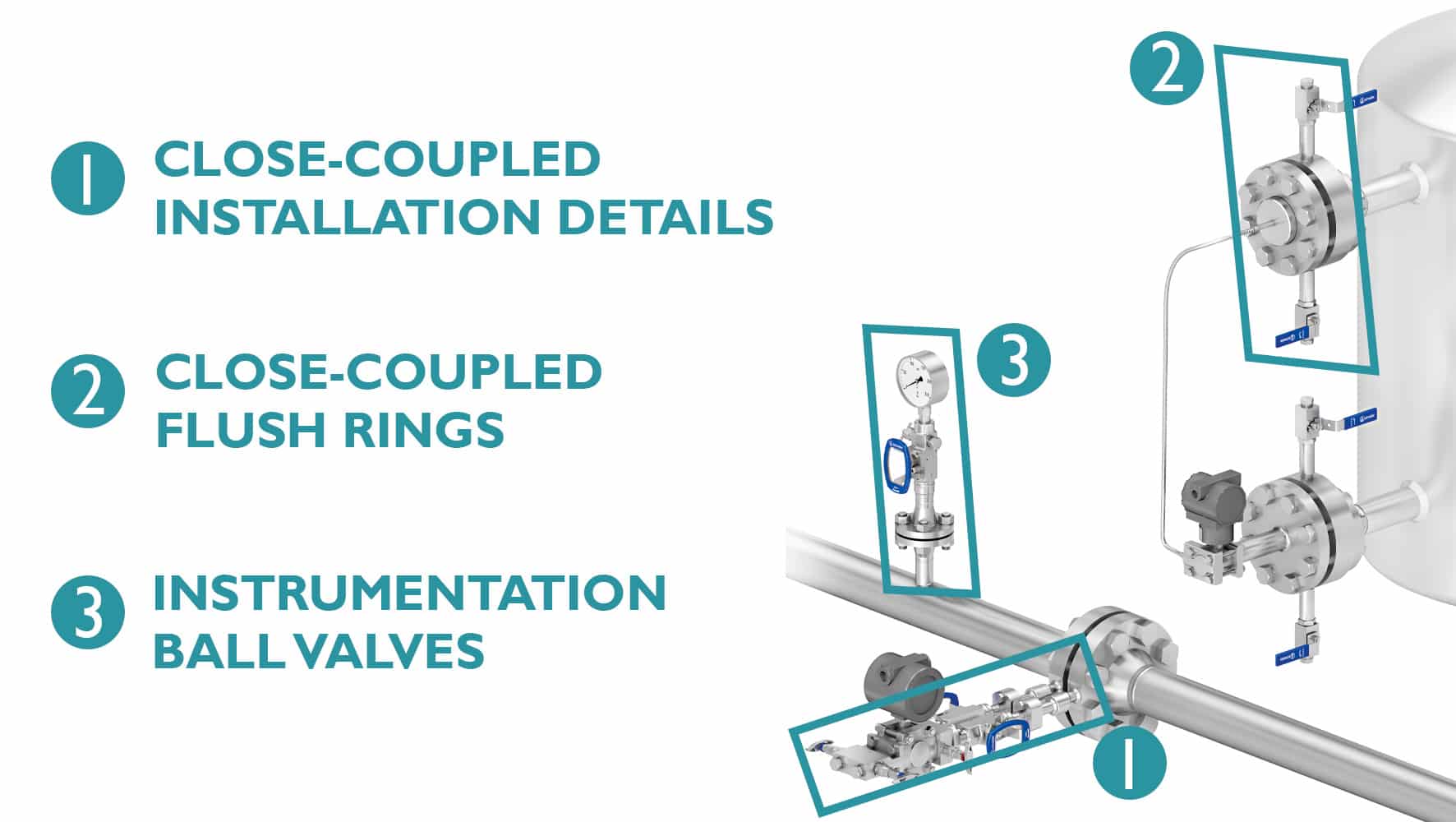
Example of a close-coupled installation.
You can take your pick from a range of options to suit your specific application. Keep both eyes open when choosing instrumentation ball valves. They are heavily influential in lowering the likelihood of fugitive emissions. And mark the difference between safe and accurate measurements and lousy ones.
Remember, with close couplings, impulse piping is no longer in the equation.
Your operators will thrive knowing that!
What savings opportunities deliver close-coupled installations?
With close coupling, you achieve to save time and money on installation, testing, and as well while operation. Plant builders should be overjoyed to present operators with a solution that improves their TCO in such a way while also sparing them from setbacks.
How will those savings reflect on the EPC project’s budget and execution timeline?
The selection of close-coupled installations can help your project by:
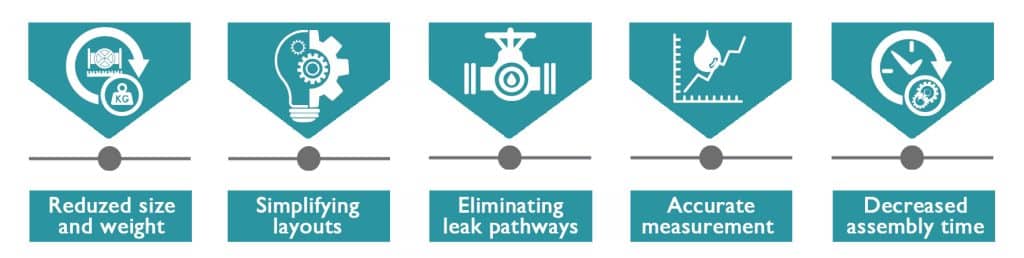
- Reducing the size and weight of the facility;
- Simplifying the instrumentation, mechanical, and civil layouts;
- Eliminating potential leak pathways;
- Increasing the accuracy and repeatability of the measurement;
- Decreasing the time and effort needed for site assembly.
Tips to approach the technology selection process
Project engineers strive to define the asset’s lifespan from design to decommissioning. With such a broad horizon, the safest way to make solid decisions for the project is by running a TOC-oriented analysis instead of a CAPEX-driven one.
A TCO-thorough study considers CAPEX and operating expenditures (OPEX), plus maintenance costs, energy costs, environmental costs, and disposal costs over the entire life cycle of the asset. This coverage promotes the comparison of different alternatives before selecting the most fitting option.
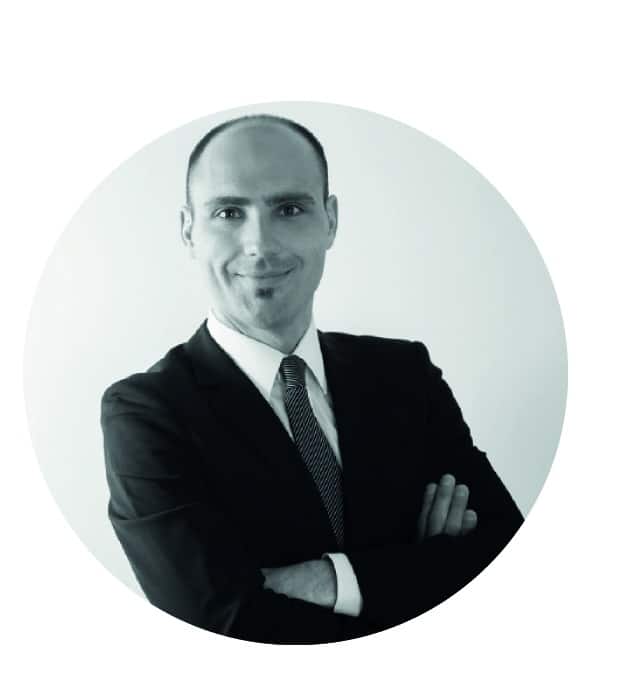
How do you know if you are on the right track? When the project’s targets and stakeholder expectations meet.
Get ready for your next EPC project
From what we’ve seen, a close-coupled installation gives you an edge over a conventional one. So, if you are in the middle of sending a technical and commercial proposal for your next EPC project, you can use these cues to reinforce your measuring system offer for close couplings:
Design and construction
( a ) Installations are available in a huge variety of options.
( b ) Elimination of plugging of long impulse lines, improving system reliability.
( c ) Elimination of threaded- but also connections in general, support fewer fugitive emissions.
( d ) No coordination of multiple suppliers and orders is needed.
( e ) Most of the valves and manifolds are soft seated and therefore fully roddable.
Pre-testing
( a ) No pressure test of the measuring line is necessary.
( b ) Shop testing reduces costs.
Pre-assembly
( a ) Less site work and lower installation costs (only for welding and assembly of transmitters).
( b ) Avoid duplication and manpower for on-site coordination.
( c ) Delivery of fully-welded ball valves (fewer potential leak points minimize fugitive emissions).
Outro
All too often, the tiniest details end up having an enormous impact on our lives. It happened to our operator clients when they received the plant. At the time, they were unaware of the crucial role a peripheral like a conventional measurement installation would play in their final product. After serious maintenance spending and no improvement, they were searching for improvements and were able to:
- Switch technologies from conventional to close-coupled installations,
- Maximize reading accuracy to make the right call for their process,
- Remove impulse lines from their day-to-day, and
- Lead their operations with confidence.
In other words, they saw a golden ticket to leave a stale situation and took it.
Plant builders want to install enduring plants that don’t face recurrent failures. Fulfilling such a job requires substantial efforts that only end after a successful custody transfer to the operator. Close-coupled installations contribute to accomplishing this stellar closing.
So, dare to try new and effective technologies. If they request a slightly higher investment, look at the total cost of ownership. Run the numbers. You’ll see the operators gain juicier benefits over time.
At AS-Schneider, we have implemented close-coupled installations for years. Together we can realizing specific solutions for your application.
Let me know if you need support.
Until next time.
Image Source: © Olga, zaurrahimov (Adobe Stock) & AS-Schneider