Sealing solutions for valves: Types, materials and applications
When working on an EPC project, defining the operating conditions, process constraints, and service type for the valves becomes easy. Nevertheless, selecting the right sealing material can be challenging without support from your chosen vendor.
Which components and materials does your valve sealing truly require? Additionally, what potential cost implications might arise from your choice? These uncertainties loom.
Inside this article, you will find insight to improve your valve selection process by learning more about sealing materials. Moreover, once you are done, you will know what sealing attributes to consider when buying your next valve.
With my experience at AS-Schneider Group, I can help enhance durability and prevent leakage issues. Thanks to my deep understanding of valves and sealing materials, I can provide valuable insights.
Let’s begin.
Valve design is the first step to a reliable process
Present throughout process facilities, valves are a fundamental necessity, and for good reason. And rightly so. For that reason, without valves, there’s no way to guarantee safety, efficiency, or quality. They play a critical role in the everyday goal of maintaining a steady and efficient performance.
When plant operators arrive at the facility, they jumpstart each shift by going over relevant process parameters. Based on this status, they call the shots from the control room or directly at the site. Their ultimate goal is to lead the plant into a normal performance range.
During these interventions, plant operators rely on valves as a means to:
- control, isolate, or depressurize fluid across the plant’s equipment, pipes, and units;
- protect assets and people from hazards (overpressure, leakage, or fire);
- sustain desired process conditions and product consistency;
- and switch operating modes when needed.
Consequently, these tasks have undeniable consequences.
Importance of a precise valve design
The significance of an accurate valve design at the EPC project stage cannot be overstated.
Plant planners are well aware of the situation. Thus, when building the project schedule, they consider the completion of the valve design as a crucial milestone. Especially if they are placed as long-lead items. To take charge, instrumentation engineers lay the groundwork to profile each valve. Then, they continue to run sizing calculations and draft specifications.
However, in the valve specifications, the sealing material details tend to be blank or underspecified for the vendor to jump in. In my experience as a valve solution provider at AS-Schneider, this has been the case.
That’s a practice you can reinforce for your own good.
The impact of seals on reliable valve performance
Now let’s address the effects of seals on the reliable operation of valves.
Needle valves with metal seals for a large temperature application range. On the other hand, ball valves with soft seals for a ‘usual’ temperature range. Alternatively, ball valves with metal seals for high-pressure and high-temperature fluids.
As you can tell, those are three examples of valves and their seals for different applications. In each case, much like the valve itself, the seal changes according to service.
But why is that? What does it mean for your process?
Seals are crucial in engineering to prevent substance transfer. Notably, they stop gases or liquids from escaping through cracks or porous surfaces in valves, machinery, or pipes. Without a doubt, a defective or absent seal leads to process stream leaks, environmental damage, and potential harm or death to living beings in the area.
In simpler terms, tightly sealed valves:
- protect the mechanical integrity of your valves;
- help keep facilities and nearby areas safe and clean by preventing leaks;
- and avoid process contamination (from the outside into the process).
While planning your plant, you always want to end up with the right sealing solution for your valves. To choose the top seal option, you must consider several factors. Before we get into that, let’s address the kinds of seals available for your applications.
Types of seals for valves
Seals are inextricably linked to the functionality and durability of your valves. Given the variety of valve options and applications, it is only natural for seals to have different variations as well. In this way, they can match the valve’s purpose and mechanical design with intent.
In such a context, three types of seals are available to complement your mechanical valve design:
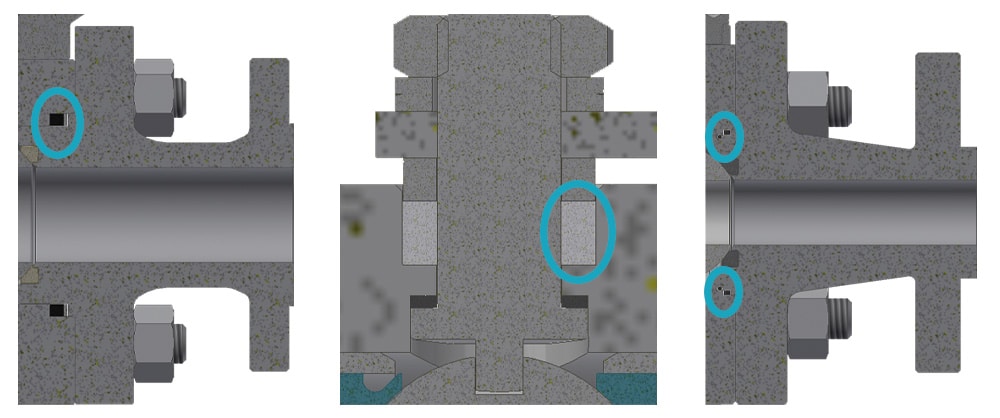
Firstly, static sealing
When a seal is not meant to experience any relative motion between the sealing surfaces or edges, you are in front of a static seal. Applications without movement include flanges, plugs, or tubing. In the manufacturing shop, a static seal is built between two fixed and sturdy surfaces. The connection between the body and the flanges of the valve is a classic example.
Static seals can be either axial or radial, depending on the direction of compression. Furthermore, they act like a gasket and are usually made of rubber or metal.
In this context, it is worth mentioning that O-rings stand out as a frequently used static seal.
Secondly, dynamic sealing
If your application calls for rotation, oscillation, or reciprocation between the hardware and sealing solution, you will need a dynamic seal. In contrast to its static counterpart, a dynamic seal works by creating a barrier between stationary or moving surfaces.
Dynamic seals serve the purpose of preventing fluid leakage, blocking the entry of contaminants, and minimizing pressure loss.
At this point, do not forget that these seals come in two different varieties:
CONTACT
CLEARANCE
The choice between them depends on whether they have rubbing contact with the mating surface or not. For example, if you look at the valve stem design, you’ll notice how the system stays oil-free while ensuring tightness during movement. This is a typical example of a dynamic sealing solution in action.
Lastly, double sealing
Finally, you can count on a third mechanical seal option for your valves: double sealing.
What makes a sealing double? Well, it’s when there’s a sealing face positioned on each side of the shaft. This array adds redundancy and reliability in applications where fluid leakage is unacceptable or hazardous. Moreover, a double seal is also a go-to-choice when the design clearly needs the prevention of contamination.
Double seals can operate in tandem mode (both seals share the same pressure) or buffer mode (the inner seal has a higher pressure than the outer seal). In addition, the use of a primary and secondary seal further increases the tightness and safety of the valve, regardless of whether they are static or dynamic. The material combination allows the positive properties of both to better serve their purpose.
A good example of a double sealing system is the combination of an O-ring (primary seal) and a graphite packing (secondary seal). In case of fire, the O-ring would be damaged by the heat, but the graphite is heat resistant and ensures tightness in this case. Under normal conditions and temperatures, the O-ring (with much smaller dimensions) would provide additional sealing for the application, with a secondary seal material.
If your application relies heavily on double sealing, I have great news for you. The latest developments are reducing their necessity based on the results of tightness tests run according to ISO FE class AH for graphite packing.
What does it mean for your design? It means, that additional O-rings on the valve head units are no longer necessary.
High pressure and sealing
High pressure and sealing can have both positive and negative effects on sealing performance.
On the positive side:
- Increasing pressure enhances sealing in two key ways. Firstly, it enlarges the contact area between the gasket and the flange, leading to improved sealing.
- Secondly, it reduces the leakage rate through the gasket.
On the negative side:
- Conversely, the downside is that higher pressure can stress the gasket material, potentially causing deformation, damage, or failure.
To mitigate the adverse effects of high pressure, it is crucial to identify the optimal pressure range. Within this range, sealing will be both effective and reliable.
Mechanical seals for your valves
Once you’ve determined the suitable sealing type for your applications and assessed the pressure impact, the next step is to explore various mechanical sealing options. There are several types of mechanical seals designed to prevent leakage. Each with its own advantages and disadvantages depending on the application, operating conditions, and cost.
Among the leading options for mechanical seals for valves are:
O-rings:
Made with HNBR, FKM, or FFKM, these mechanical gaskets are characterized by a circular cross-section used to seal two or more pieces together. O-rings are preloaded in your application, considering fitting tolerances.
Packing:
Another type of mechanical gasket that is typically fabricated with PTFE. When compressed between two or more parts, they create an effective seal at the interface.
Lip seals:
This pre-stressed mechanical accessory can also be called a rotary shaft seal or oil seal. Here are two valuable tips you should be aware of to enhance their performance:
1) Always consider that they compress better with increasing pressure.
2) Make sure they are applied to an appropriate surface to seal.
Bellows:
They are incredibly resistant to high temperatures up to 550°C, ensuring extreme tightness. Because of that, valve bonnets with bellows seals are often used in applications where the highest tightness class is required, e.g., for toxic substances, in vacuum technology, or in the nuclear sector.
In the next four images, you can see how the mechanical seals (O-rings, packings, lip seals, and bellows) are placed in the hardware.
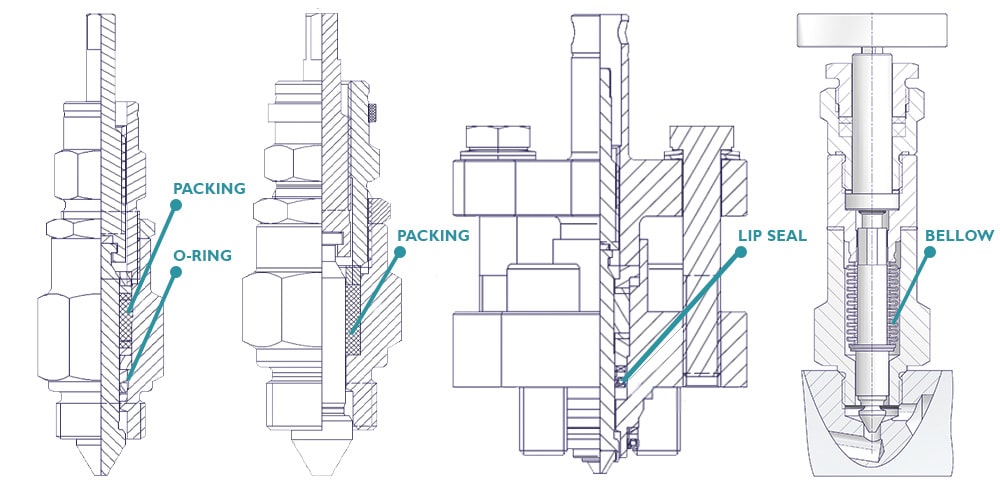
Double sealing (o-ring and packing)
Single sealing (packing)
Representation of a lip seal
Representation of a bellow seal
The effectiveness of your sealing solution is subject to the materials you choose. Thus, asking for compatible materials in your mechanical seal ensures success in avoiding the passage (or leakage) of fluids, gases, dust, or other contaminants through gaps or joints.
Should we get to know who these famous materials are? I vote yes!
Sealing materials for valves
Your choice of sealing materials is contingent on several aspects. Here, we overview their operational range and main applications.
Without further ado, these are some of the most commonly used sealing materials for valves:
Material Type | Description | Typical valve temperature range* |
---|---|---|
PTFE (Polytetrafluoroethylene) | • Soft textured • Qualifies as seat material and packing material. • Often combined with carbon (RPTFE) to increase stability | -200°C up to 260°C |
PEEK (Polyether Ether Ketone) | • Strong plastic quality • Mainly used as a seat material • Often combined with PTFE (modified PEEK) to enhance elasticity and improve adaptability | -60°C up to 260°C |
HNBR (Hydrogenated Nitrile Butadiene Rubber) | • Common O-ring material • Low temperature range | -55°C up to 150°C |
FKM (Fluorine Kautschuk Material) | • Used as an O-ring material • Great chemical properties • Large temperature range | -50°C up to 232°C |
FFKM (Perfluoroelastomeric Compound with High Fluorine Content) | • Premium O-ring material • Very high temperature resistance • Depending on composition, it might offer excellent resistance to aggressive media | -15°C up to 325°C |
Graphite | • Common packing material • Temperature insensitive • Well suited as a fire-safe seal | -200°C up to 538°C |
* Temperature range depends on valve type, application range and seal material compound!
In general, it is difficult to give such a general temperature specification for a material, as it always depends on the specific application. Ball seats made of PTFE, for example, cannot be subjected to such a high temperature as a chambered packing.
Outro
To summarize, the careful selection of sealing materials for your valves is vital for ensuring the reliability, safety, and performance of your process plant. It is crucial to familiarize yourself with various seal types, including static, dynamic, and double seals, to make well-informed decisions.
Additionally, considering the pressure impact and exploring mechanical sealing options like O-rings, packings, lip seals, and bellows helps improve the effectiveness of your sealing solution.
Lastly, familiarizing yourself with common sealing materials such as PTFE, PEEK, HNBR, FKM, FFKM, and graphite enables you to choose materials that are compatible with your specific application.
By prioritizing sealing materials in your valve specifications, you can enhance the durability and prevent any leakages in your process plant.
My personal tip to you: In a few weeks I will publish my 2nd article here in our blog. This one is about: 10 features to consider when selecting sealing materials for valves. So, check back now and then.
Image Source: © visoot (Adobe Stock) & AS-Schneider