Asset performance management of mechanical components by industry 4.0 app
Building a new facility or upgrading an existing one is a high-stakes mission. Even with modern technological and mechanical advances, there are thousands of tasks to juggle. Each is imperative for the delivery of an asset that withstands the site conditions and the challenges of daily operations.
Plant builders, as per usual, play a vital role in getting everything up and running. They gather approvals and select the right contractors and suppliers. They also set the basis for effective asset management throughout the lifecycle. By today’s standards, that means crossing over to “industry 4.0” to analyze asset performance based on data.
Are you ready to scrutinize your plant beyond what’s tangible? Does the concept intimidate you? Or maybe you started but haven’t seen the benefits yet?
Regardless, you’ve come to the right place.
I will explain how an industry 4.0-enabled asset performance management (APM) app works. And show why it is a powerful resource to empower operations and maintenance. The possibilities are endless through “bad actor” identification in a sea of data.
Plant engineers, operators, and digital teams don’t want to miss this one.
So, without further ado, let’s begin.
The challenges of managing industrial assets and mechanical components
“How can I cut downtime?” That is the perennial question from my operator customers at AS-Schneider.
Some have been as prepared as they can be:
- developing a comprehensive asset management plan with detailed maintenance schedules;
- managing the logistics to maintain and repair equipment and accessories with well-trained personnel;
- ensuring that all devices are up-to-date and calibrated; and
- securing compliance with industry regulations and safety standards.
But something always goes wrong. Usually when you least expect it.
For example, one morning, in pouring rain, a client told me about a failing valve from a competitor. It turns out that the same valve was a recurring offender, one of the “bad actors.”
The issue deepens when there are losses in data traceability and accountability. A factor that happens when the integration between systems is not seamless. By systems, I mean the four main components deployed to safeguard industrial facilities:
#1. BPCS
Basic Process Control System
#2. SIS
Safety Instrumented System
#3. PLC
Process Logic Controller
#4. CMMS
Computerized Maintenance Management System
What can you do?
Repurpose your approach toward asset management.
Goals of industrial asset management
The industry is undergoing several changes. The infrastructure is aging. Regulations keep getting tighter. Qualified workers are scarce amid the ongoing retirement wave.
Yet, two constants remain:
- The need to make processes more agile, productive, and sustainable.
- The push to reduce risks, downtime, and, of course, OPEX.
How can plant crews handle the dynamic situation without losing focus?
Customized asset performance management strategies are the solution.
Since I specialize in valves, I’m going to set an example based on them.
Example: Five performance elements of valves
With an industrial valve, you want to manage five performance elements: reliability, safety, efficiency, cost control and lifespan.
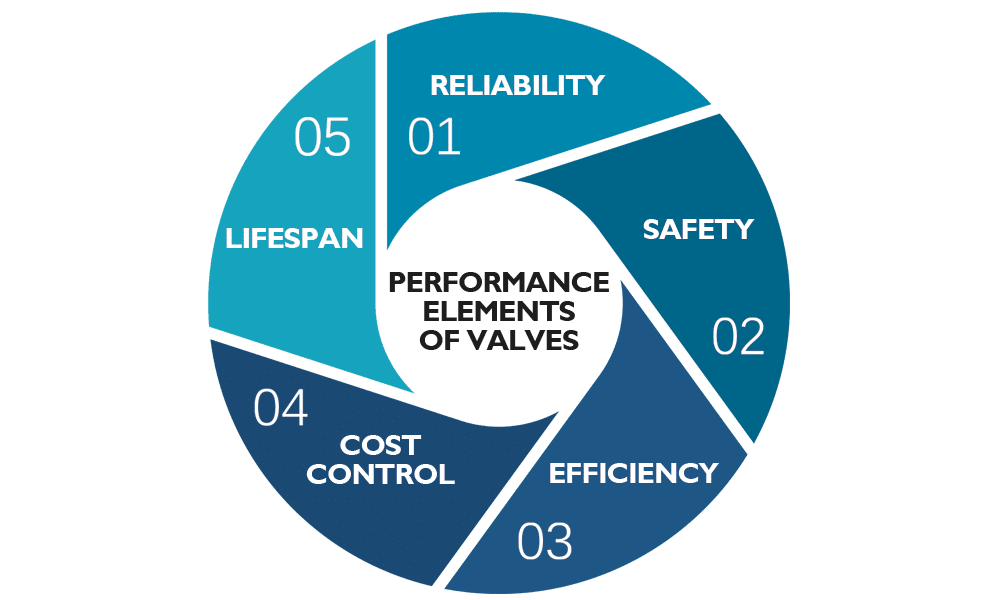
Infographic: Five performance elements of valves
A healthy valve that operates optimally is less likely to fail. It has lower energy and repair requirements and higher reliability and uptime.
To keep a valve healthy, routine inspections and maintenance are necessary. They help to prevent premature wear and tear and extend valve life. Reinforcing their practice is the one-way ticket to ensure the valve stays far away from initiating accidents.
I’m sure you know most of this. I also know that you spare no effort in supporting regular maintenance with the resources at hand.
So why do you feel like fighting an uphill battle?
Unlike in my example, you don’t have a single valve to guard. You have dozens of individual assets spread across scattered locations to look after. With those many assets and limited personnel, there’s too much to handle.
It gets tough to define hierarchy and priorities. Regular check-ups lose relevance. Everything starts to seem like an emergency. You are becoming reactive.
So let’s touch down on how the APM software can turn that entire prospect around for you. On how it can make goals more reachable and infuse peace of mind.
What is an APM platform?
In a nutshell, asset performance management is a strategy put in place to administer the main components of an enterprise.
Within an industrial context, it is a software that collects live data from sensors attached to critical field devices with the goal of improving asset management. Instead of going blind, stakeholders get the support of sorted data.
At this moment, APM is a primary enabler of digital transformation. A medium where traditional asset management practices and new digital technologies meet. Such an interface fosters advances in reliability, maintenance execution, and business performance.
APM is also compatible with other systems, such as PLCs and CMMS. That means the software can cross-reference the data available on the asset. Because of that, the results are thorough analyses narrowed down from a single source of truth. What else is possible? They predict the likelihood of failure.
Let’s set an example. I am responsible for maintaining the pressure control valves (PCV) at ten dispersed primary oil stations. How can APM boost my process?
For starters, I can make proactive decisions on the assets’ upkeep. Based on each PCV’s health status, use rate, and maintenance requirements, I can be more secure in planning the interventions. Before proceeding, I must review the available condition-based monitoring, predictive failure, and probabilistic risk models. By the end, my client gets to avoid expensive downtime and ensure the integrity of the assets.
As you can see, APM is a resource that allows the operational management team to lean toward a digital transition. It is an aid to welcoming new roots that generate gains in production and optimize maintenance.
What are the components of an APM platform?
I like to think of the asset performance management platform as a physician. The stakeholders consult it to learn about the asset’s health. The examination reveals potential issues and cures. Stakeholders take care of the treatment. No critical problems should unfold.
Does it seem too good to be true? It won’t once you learn what’s behind this life-saving solution.
The APM platform is a product of industry 4.0. It collects data from IoT sensors, maintenance records, and other operational systems. Advanced analytics and machine learning algorithms do the rest. By that, I mean generating leads and issuing recommendations.
The structure for processing big data follows this analytics framework:
- Descriptive: a collection of historical data to identify patterns.
- Diagnostic: analysis of data to understand why something happened.
- Predictive: statistical and machine learning algorithms analyze data to predict future outcomes.
- Prescriptive: data analysis and machine learning algorithms show future actions.
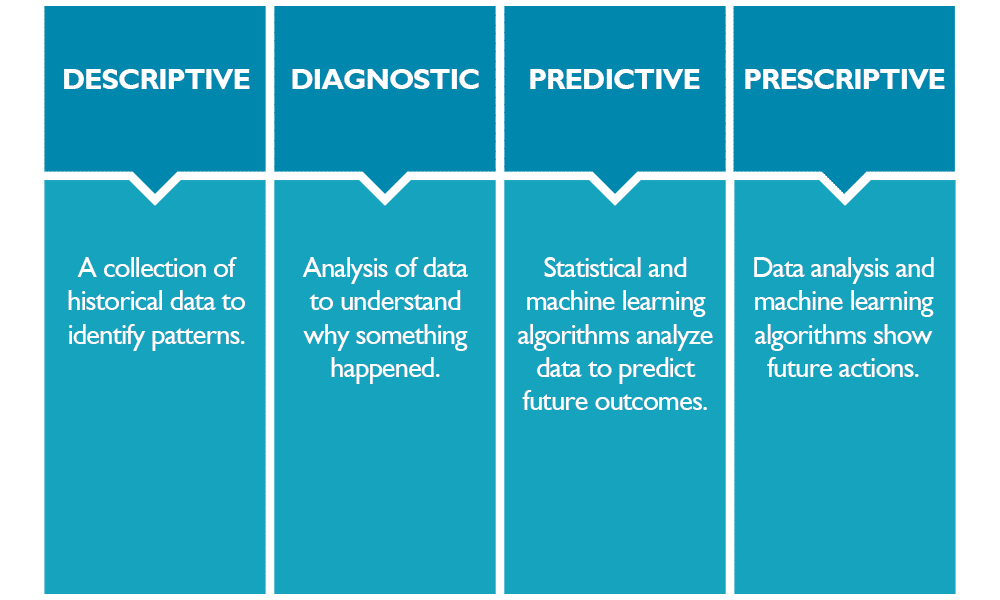
Infographic: Structure for processing big data (analytics framework)
How does this apply to a real world full of assets?
You can now pursue condition-based monitoring using accurate data on the actual state of the asset and roll in predictive maintenance actions. Soon, you will be out of the reactive zone and ready to thrive, beating asset failure.
What are industry 4.0 apps in the context of the APM?
Since automation began, production plants have become places where data is rampant. The logical next step was to find agile mechanisms to understand data better and seek profit from it. That road led us to live in the fourth industrial revolution, or industry 4.0.
This industrial era marks the transition from automated processes to the use of automation with data exchange. IoT, AI, robotics, machine learning, and cloud computing are the pillars of this current stage. The integration of these technologies leads to the development of industry 4.0 apps, which are designed to improve efficiency, productivity, and performance.
So to answer the original question. What is an industry 4.0 app in the context of APM? It is a piece of software used for gathering and saving intelligence on an asset to improve reliability and efficacy based on real-time data analytics.
Does this concept ring any bells?
That’s why earlier I referred to the APM platform as a product of industry 4.0.
Who are the stakeholders of these industry 4.0 apps?
Stakeholders are individuals or groups with a vested interest in the success of a business, industry, or project. Their role in connection with industry 4.0 apps changes according to their involvement:
Plant owner
Developers
Pant engineers, operators, and managers
Groups supporting
the app development
They nurture the need for the apps to streamline production processes, reduce costs, and increase output.
They are responsible for creating and maintaining the software that powers the apps. Without their expertise, obtaining benefits would not be possible.
They are end-users who interact with the apps on a daily basis.
They can be from a technical background or a funding investor.
The diverse group of stakeholders helps to drive the adoption of industry 4.0 and usher in a new era of manufacturing.
How are industry 4.0 apps connected to the data of the process plants?
We have reached the million-dollar question, haven’t we? Let’s dive in.
The connection between industry 4.0 apps and process plant data is possible through advanced communication protocols. OPC UA, MQTT, and RESTful APIs are the most used for this purpose. Your digital team for sure knows them. The communication protocol enables seamless integration between different systems and devices. Because of that, data sharing and analysis can occur in real time without fault.
There are a couple of serious notes that you should know about this method, though.
First, setting up interfaces between the host (the developer) and the user (the plant owner) takes time.
Second, and most importantly, since the host is the app developer, third-party involvement is implied. That means the data leaves the asset owner’s infrastructure.
If you’d like to avoid data sharing, you have other alternatives:
- Install the Industry 4.0 app on an edge computer. This method requires the app to be close to the machine itself. Therefore, it reduces latency in data transfer and network bandwidth consumption. It also enables less dependency on cloud services.
- Package the app using a service that facilitates set-up, like Docker. By this means, the asset owner adds the app to their infrastructure without extensive technical knowledge or support.
Based on your own reality, you can choose the best option to connect any industry 4.0 app with your process data.
Why should an asset owner want to share data with his supplier of mechanical components?
Working at AS-Schneider has given me a unique perspective on the benefits of data sharing between asset owners and suppliers.
Though it may seem like a risky move, in reality, it can be a bold, win-win strategy that benefits all.
From a collaboration point of view alone, data sharing leads to:
- Improved communication between parts.
- Enhanced customization of products or services based on actual operational performance data.
- Joined efforts to analyze scenarios and identify potential issues.
- Proactive participation for informed decisions about arising issues.
- Instant awareness of changes or updates that could affect component performance.
- Quicker post-sales support.
Asset owners have the power and means to limit the information they share with the supplier. They also have the tools to estimate how much profit they can gain from the collaboration benefits listed above.
So, instead of shutting the door on this opportunity, I encourage asset owners to run the numbers. To see how much extra value there is to gain. Those figures should be the indicators dictating a final answer.
Conclusions
Managing industrial assets has never been a more challenging and dynamic endeavor than it is today. Modern plant stakeholders find themselves dealing with:
- aging assets,
- harsh operating environment,
- labor shortages,
- tighter regulations,
- sustainability demands, and
- higher costs of maintenance and repair.
Not the most encouraging panorama.
However, with the right strategies and tools in place, they can turn that gray landscape around and infuse it with color.
Industry 4.0 apps like the APM platform are a booming trend because of that. They are powerful artillery to defeat such headaches so operations teams can start seeing the grass greener on their side.
Adopting a new asset performance management process bolstered by condition-based monitoring and predictive and prescriptive analytics makes “bad actor” eradication doable. Asset managers can tip the balance in favor of proactive practices that increase uptime, spare incidents, and boost asset value.
The solution can also bring asset owners and their suppliers closer together. Live feedback and direct collaboration open the door to enhanced product or service customization.
All in all, if you are a stakeholder in a plant seeking a new solution to rock the chains, this might be it for you. So, think about it.
Image Source: © Blue Planet Studio (Adobe Stock) & AS-Schneider