5 important facts for a safe and transparent (remote) third-party inspection
We are all facing many restrictions due to the pandemic. Therefore, we need to find ways to still provide the best possible support to our customers. One digital service that our customers can use is our third-party (remote) inspection for a visual inspection to check the valve quality before shipping.
To be on the safe side and make sure you think of all the points in your next third-party inspection or remote inspection, I’ve summarized the most important facts for you in my new blog article.
1# Why third-party inspections are made
The use of third-party inspection provides an unbiased, professional perspective for customers. They
can do this inspection by themselves before delivery. Or they can do it with the support of a certified inspection company. In this way, the customer gets an eye-witnessed confirmation. They have the certainty that the product will be 100% in line with their specifications.
2# Inspection during machining and assembly process
One important fact is that a third-party inspection does not only have to take place at the end of a production process. The customer may also request a remote inspection of the valves already during the machining and assembly process to inspect remotely the individual components of a valve/manifold. This could happen by performing several non-destructive examination (NDE) tests.
Overview of non-destructive examination tests
-
Positive material identification test
One of this non-destructive examination tests could be a positive material identification (PMI), which identifies chemical values of a material and therefor confirms the correct material has been used. -
Liquid penetrant examination test
Another typical non-destructive examination test could be a liquid penetrant examination (LPE) test which detects defects such as cracks, overlaps, wrinkles, pores and binding defects that are open to the surface. - Other important non-destructive examination tests can also be carried out
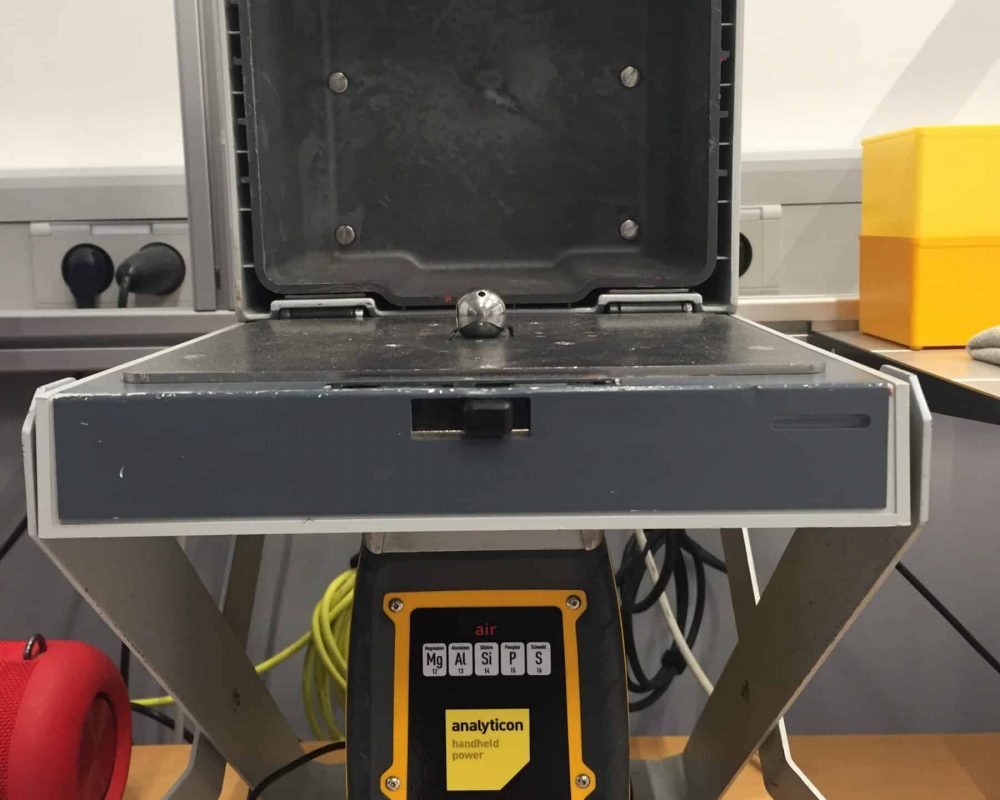
Positive material identification test (PMI)
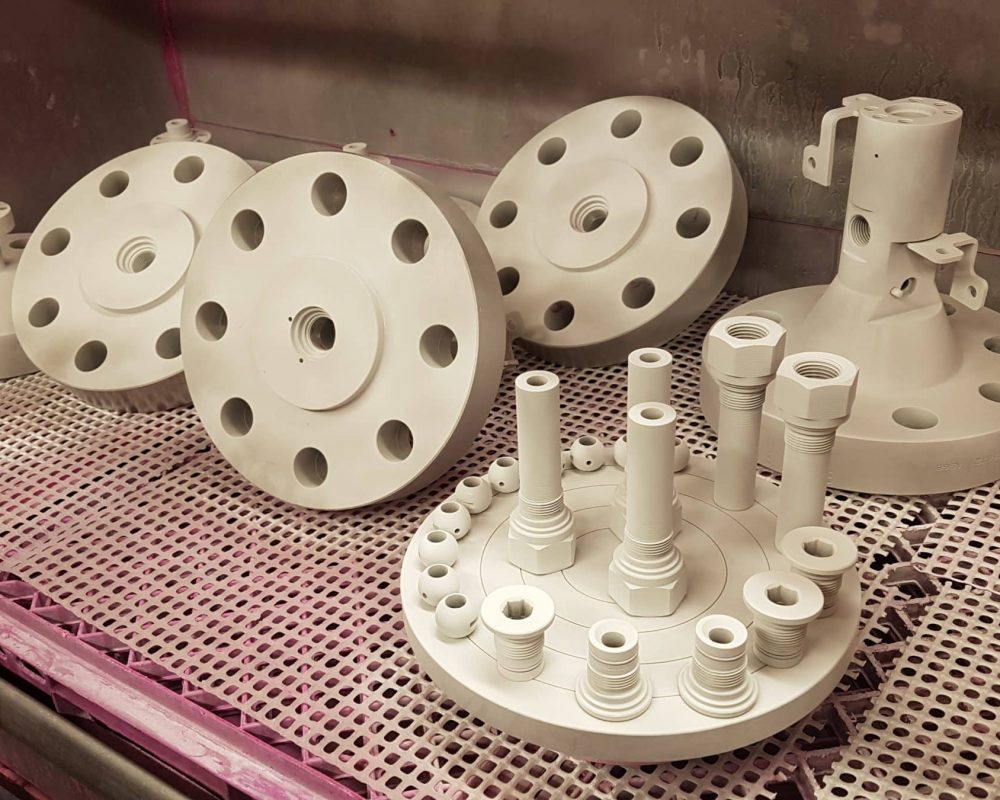
Liquid penetrant examination test (LPE)
Significant advantage of non-destructive examination tests
The big advantage of the above-mentioned non-destructive examination tests on single, non-assembled components is that any possible safety-relevant weak points can already be detected before final assembly of the valve or manifold. Once the valve or manifold is assembled, some areas and components are not accessible anymore and a non-destructive examination test cannot be performed afterwards.
The non-destructive examination tests ensure that the customer receives a high-quality product. With the testing, we can be sure that the product will fulfill its function sustainably.
Overview of other important tests
-
Pressure test - Shell test or high/low-pressure seat test
Apart from non-destructive examination testing, usual pressure tests can be realized, too. These inspections include Shell test or high/low-pressure seat test (according to EN 12266, API 6D, API 598, ISO 5208, etc.). -
Fugitive emission test
We also do the fugitive emission test according to ISO 15848-2 or MESC SPE 77/312. Shell test, high/low-pressure seat test and the fugitive emission test will be performed after full assembly of the valve or manifold.
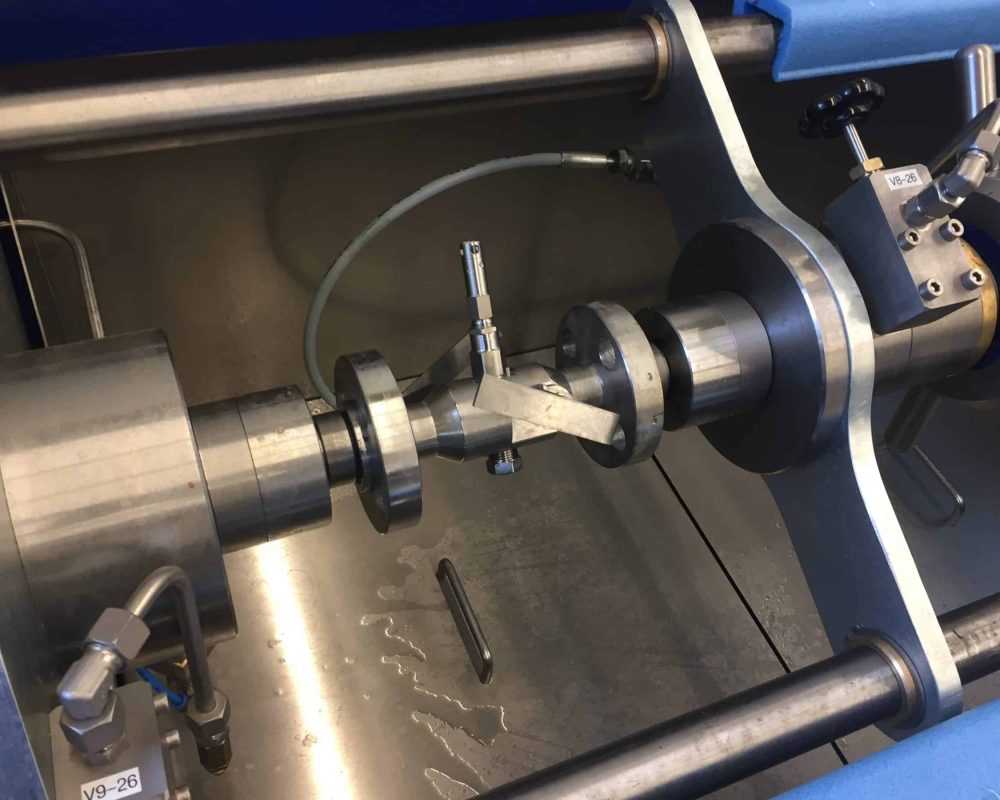
Shell pressure test
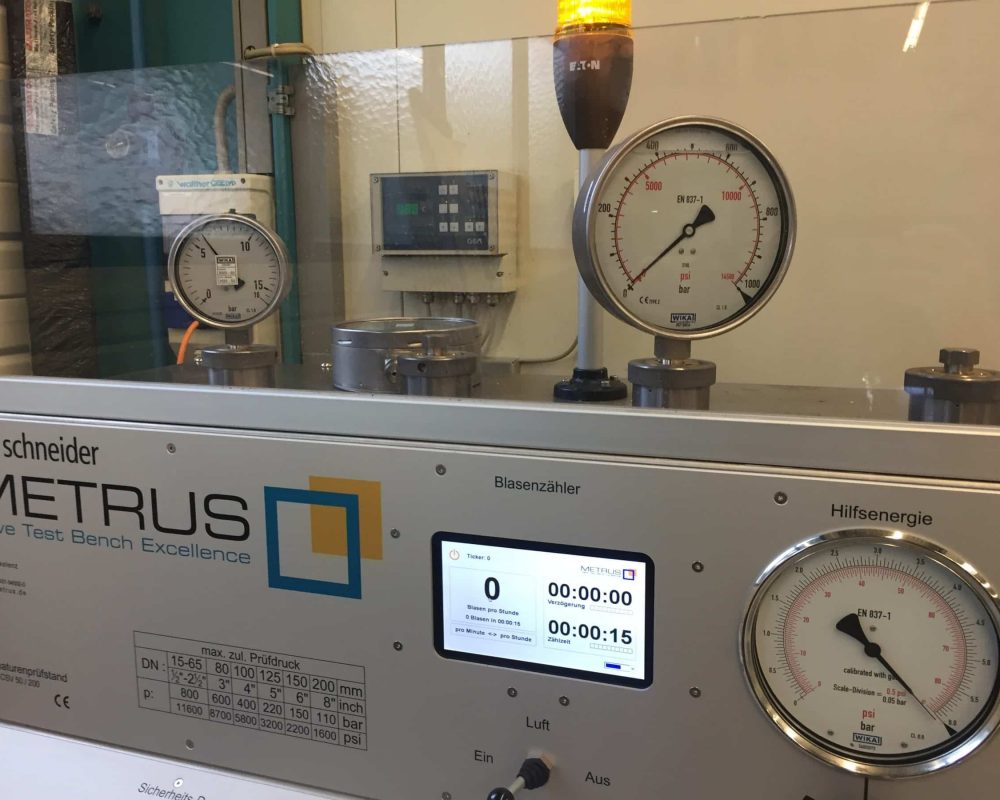
Seat pressure test (air)

Fugitive emission test
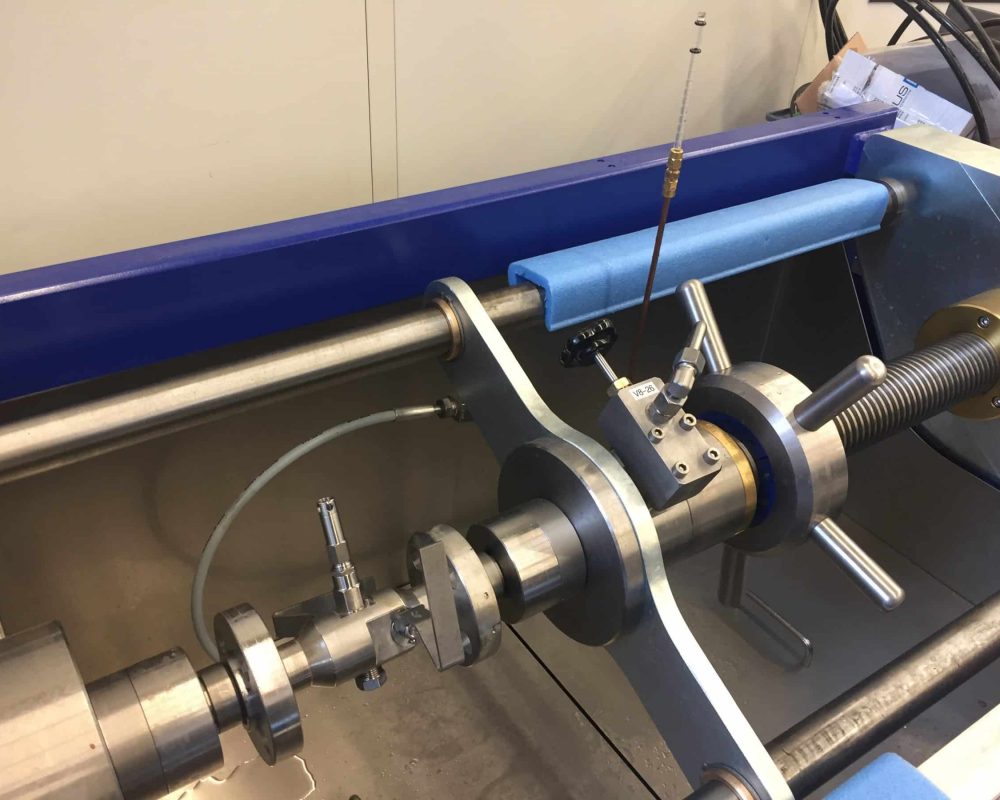
Seat pressure test (water)
Further to the equipment, we also have certified personnel on board who can carry out the ISO FE Test according to MESC SPE 77/312, for example.
3# How is a third-party inspection done
The customer should first define how they want us to do the third-party inspection. We recommend a prior consultation so that the customer can tell how the third-party inspection should proceed and what exactly they would like to see.
In the case of the remote inspection, the customers should decide if they wish to have only pictures or whether they want us to make remote videos of the ongoing inspection steps that have been agreed in advance and regulated in the inspection and test plan. In this case, the customer will receive the taken pictures and remote videos of the required test steps and can check the results afterwards.
The other option is a live and safe remote visual inspection. Our customers can be either present via MS Teams, GotoMeeting or Skype or other digital platform. And can therefore follow any kind of testing live.
4# Who are the auditors during a third-party inspection
In the case of a third-party inspection is not carried out remotely, external inspectors from specialized inspection companies are assigned to carry out the inspection on our site.
During the inspection period, at least two AS-Schneider employees are available. They guide the external inspectors during the verification of the required tests and audit steps.
5# How long does a third-party inspection take
Generally, the duration of a third-party inspection always depends on the product. It also depends on the required scope of testing. The third-party inspection takes one day on average. But it can also take up to a week or even longer.
Your benefits of a remote third-party inspection
We’ve gone through quite a few challenges in this article. The following list outlines the significant benefits of carrying out a remote inspection:
-
Non-contact work (protection of staff and customer)
A remote inspection allows contactless work. This policy protects our employees, the external inspectors, and the customer, too. By reducing contacts, we can prevent infections. -
Elimination of travel time and costs
A remote inspection not only cuts an external inspector's cost. It also saves time for traveling and thus costs as well. -
Faster third party inspection procedures
The elimination of external inspectors increases flexibility. It may even reduce the inspection lead times.. -
Video solution (traceability/documentation)
Also, a remote inspection provides traceability. It provides customers with the ability to witness the agreed-upon steps as we inspect them.
The benefits of utilizing remote third-party inspections are many. These inspections are beneficial during this global pandemic. They far outweigh the challenges. They are of utmost importance, and they show that we are doing our part to curb the spread of COVID-19. As a company, we, and our customers, need to adapt and embrace the “new normal”. Remote third-party inspections are but one of the smart ways that make it possible.
Image Source: © Blue Planet Studio (Adobe Stock) & AS-Schneider